Flash and JavaScript are required for this feature.
Download the video from Internet Archive.
Description: This lecture covers line defects, which are one-dimensional defects in a crystal that affect macroscopic materials properties such as deformation.
Instructor: Jeffrey C. Grossman
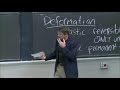
Lecture 24: Point and Line ...
So today, we're going on from zero dimensions to one dimensions, and we're talking about line defects in order to understand what they mean.
We're going to contextualize it in terms of stress/strain curve.
So we'll talk about that.
And all of this is called the dislocation.
So that's our goal for today.
Now, on Monday, after lecture actually, a student came up to me and asked a really good question.
And it was related to the Hume-Rothery rule.
Remember, on Monday, we talked about point defects, zero dimensional.
So you have a localized disturbance in the lattice-- of vacancy.
You take it out.
You can have that occur in a material that's ionic.
Not a metal, but maybe an ionic material.
And then you got to think about charge neutrality, Schottky and Frenkel.
And then we talked about substitutional defects, which would be where you take an atom out of the lattice and you put another one in.
And Hume-Rothery, I mentioned, had come up with some empirical observations and so I listed these.
So he studied a class of metals and came up with these general guidelines.
And as with so many things that we've learned so far, these are general rules that get broken sometimes.
So the question the student asked was a very good one.
Said, well, if the valence of something you're trying to substitute into something else has to be the same or higher, how does p-doping work?
How does a p-type semiconductor work?
That's a really good question, right?
Because the valence is lower, by definition, that's how you make it p-type.
A-ha.
So my response was, well, because Hume-Rothery was designed around metal, I'm not sure how much of these apply to semiconductors.
Although for semiconductors, you do want to make sure the sizes are similar, at the very least.
But that got me thinking.
And so I went and I read some papers last night.
Here's one on the valence effects and relative stabilities-- valency effects.
So this is from the '80s and I just wanted to cite something here.
So here they say almost a half century ago-- so that's Hume-Rothery, so it's the '80s or the '30s-- pioneered the study of the effect of valency on metal alloy phase equilibria.
They found that a lower valence metal, like silver, had only a very small solubility in a higher valence element, like antimony, but that the solubility of the reverse was large.
So that's where that rule came from.
And here's the next part of this paper I want to share.
"Although the relative valency works well for that select group of alloys, it does not apply to the periodic table as a whole." So this other guy looked at 607 different systems and found that 22% of the time, the vacancy rule works, and 27% of the time, it violated the rule.
And honestly, I'm not sure we can call it a rule anymore if more times than not, it's violated.
This is a new thing for me.
So that is just to say that this rule probably is really conditional on the specific elements you're talking about.
I think the much more important ones are these three here.
The valency rule certainly depends on the system.
And all of the Hume-Rothery observations were empirical-- it's important to keep in mind.
General guidelines meant to be broken more than half the time, apparently.
[CHUCKLES]
So where were we?
But thank you for that question.
It was a great question.
It gave me some great reading last night-- materials.
Zero dimensional, Monday.
One dimensional, today.
There we are.
So that's the focus.
Now, the story today starts at MIT.
It starts at MIT in the 1940s.
Because there were these two students-- there they are, Harold Hindman and George Burr.
MIT students back then were a little bit older, I guess.
So those guys, they were in an MIT lab and they were trying to study how parachutes break.
How does a parachute break?
Because why is that an important question?
Because you don't want it to break.
Right?
And it's one of these things where you want it to never break.
Like, you really want almost 100-- so they were studying why it breaks.
So they were taking a parachute and pulling it apart, and there it broke.
Take another kind of material, pull that apart.
It broke.
This one didn't, but it's too heavy.
They were studying the relationship of the mechanical breaking to the material of the parachute.
I love that logo there.
That's the two of them in the lab at MIT pulling on a parachute.
They just have a tug of war with a parachute.
But the problem was that there was no instrument at the time that could give them the sensitivity to the force that they were pulling.
There was no instrument that could capture what they needed to make a better parachute.
So being MIT students, they built their own.
They built their own and they added a whole bunch of electronics into this instrument.
And that is where the name comes from.
It's an instrument that had a lot of electronics for the time.
Instron is the name of their company.
Instron is now synonymous with stress/strain curves.
So you go into any university, any company, you look at how-- if they need to measure something, like whether an egg breaks or not at what force, it's an Instron machine.
It's an Instron machine.
There it is-- same logo.
And because those machines give you the most accurate and well-calibrated description of the force that you're applying on this material and you can apply it very, very slowly-- so these are very common machines to look at the force you apply, to take it how much distance.
So we're going to talk about that today.
Now, we're not going to talk about it in terms of eggs.
We're going talk about it in terms of a wire.
So there's a wire.
It's a little hard to see there.
There it is.
There's another Instron machine-- this is a red one.
And here they are and they're looking at this wire.
And this wire is some material-- maybe it's copper, maybe it's aluminum.
And they're saying, what happens to this thing as I just pull it in small increments?
What is the force that I have to put on this to pull it a certain amount?
Now, that is an important graph, and it's so important that I really want you guys to understand this graph.
Because it is the way that mechanical properties of materials are first often analyzed and it's a plot of the stress, which is equal to the force per area versus the strain, which is equal to the change in the length divided by the original length.
Now, what I mean by that?
Well, let's take a wire.
Here's the wire.
There's that wire in there.
OK.
So here's a wire.
And I'm going to apply a force this way.
That's what the Instron is doing.
So there's some force being applied to it and there's some area of the wire and there was some original length.
OK.
This is called a stress/strain curve.
It's the force divided by the area that you apply to get the thing to stretch a certain amount.
Now, those MIT students were also very smart.
They knew that many materials, as you first start stretching them, the bonds between the atoms are kind of elastic.
What does that mean?
Well, it means that if I stretch it a little bit, it goes back.
Might stretch it a little bit more-- it goes back.
They're like springs.
So when you think about the deformation of that wire and many other materials, you've got this elastic regime.
And that means that it's reversible, as I just said.
Reversible.
And the displacement-- so it's reversible displacement.
If I stretch it, it goes back.
Reversible displacement only occurring under some applied force.
Applied force.
This is an elastic stretch.
If I've stretched this material elastically and I let it go and it goes back, it's like a spring.
Hooke's law is going to apply.
So Hooke's law applies.
So F equals kx or minus kx.
You can press it or-- OK.
Hooke's law.
So that means that if I start pulling on this and I start here-- so there's no stress and there's no strain, and if I start pulling on this, then I'm going to get a straight line, like that.
So that's going to be the elastic regime.
But these MIT students-- the thing is, they knew something else.
They knew that for a lot of materials, it didn't keep going like this.
It didn't keep going linearly in this nice, elastic spring way.
They knew that either the thing broke completely or it deformed-- or it started deforming.
And that is called the plastic regime.
We're coming to plastics later.
And this is a permanent shape change.
Permanent shape change.
And you can imagine, if I'm going to permanently change the shape of a material, it's got to be ductile.
So if it's something that's going to break-- remember, we talked about ionic versus metallic.
The sea of electrons allows those metals to be ductile.
And that has to do with the bonding with the electronic structure.
If you want a material to be able to change shape permanently and not crack, you need that ability to be ductile.
So there's a plastic regime.
And that makes this change dramatically.
So what happens now is, if I keep stretching it beyond this elastic regime, the stress/strain curve is no longer linear.
And in fact, it might look something like this until, at some point-- so this would be the plastic part where it's literally deforming, it's changing its shape.
And then finally, I've stretched it to the point where it fractures.
So that's called the fracture point-- you just can't pull it anymore.
You just can't pull it anymore.
And they're studying parachutes, but they knew that there were a lot of surprises out there, there's a lot of complexity in this.
And they needed to understand this regime and this regime in order to really engineer the parachute to make it better.
They had to get that data and there were no instruments that could move it and measure it and calibrate it carefully enough.
By the way, this plastic deformation that happens-- this permanent shape change, but without breaking, that happens very early on.
So there were people working, for example, with aluminum, saying, well, given the bond strength of aluminum, I predict a certain mechanical strength that aluminum could go to.
And then they find that it starts deforming 100 times lower than that.
100 times lower.
Why?
Because it enters into this plastic regime.
It doesn't stay elastic.
So what I want to talk about today is how-- I hope I've convinced you how important this is, and I'll have a why this matters on that as well.
But what I want to talk about today is how these one dimensional defects fit in with this.
How these one dimensional defects fit in.
And in fact, they explain it all.
They explain it all.
This is what the wire looks like.
When you stretch a wire and you look at it carefully, it's not just a little bit longer.
It has these very set features that occur.
It's not just deforming in any random way.
It's deforming in a very specific way.
It's deforming in a very specific way.
And so what I want to talk about is that way.
The plastic deformation mechanism is called slip.
The mechanism is called slip that leads to plastic deformation.
And it leads to that picture and it leads to the data that they got from the Instron machine.
So where does it come from?
This is a 2D picture of a lattice.
This is a 2D picture of a lattice.
So you can imagine what I've done-- oh, I'm going to hand this out.
I love this.
I can just sit and look at this-- this is so cool.
So this is a cubic-- you can think about it as a simple cubic lattice.
Here's a plane, here's another plane, there's another one.
Look at that yellow one there.
So many planes.
I got lost there just thinking about it.
I'm going to the other side.
You could get lost, too.
That's one of the planes.
That's one of the planes.
Imagine it.
Now, you notice here, I've got hanging out-- because why not?
Oh, why not?
Because there's no other possibility.
Because vacancies always exist, as we learned Monday.
They cannot not exist.
So there is one right there.
Cool.
There's an interstitial point defect, there's a substitutional point defect.
That's all from Monday.
They're just hanging out.
But here's what we're talking about now.
Look at this.
I want to take this little symbol-- this T, and I want to look at the lines that come down from it.
So there they are.
So these are now planes.
These are planes.
These are crystallographic planes.
And now, look at the other side of it and notice those same planes are following-- see to the left there?
You see how that's now a plane, a plane?
So this is actually lined up from the outside in.
It's lined up, it's lined up.
Ah!
Right here, I put an extra one in.
You see that?
That's an extra plane that doesn't go all the way through.
If it went all the way through, it wouldn't be an extra plane.
So it's sandwiched in here.
And then here, it continues over there.
That one kind of goes like that, and that one goes like that, and then they go back to the normal planes.
I have inserted a half-- if you want to think about it-- of a plane into-- right there.
Look at that.
That is called a dislocation.
That is a one dimensional defect.
It's a dislocation that is caused by putting an extra plane that stopped somewhere, and where it stops, you draw a little T in the crystal.
Oh, let's go with the mean.
Come on.
There we go.
We'll go back to this.
So that is called a dislocation.
That is called a dislocation.
That is the 1D defect.
It's called a dislocation.
It's a line defect formed by what is essentially a misregistry of atoms that gives you an extra plane.
Now, you can already see that if I put a line defect in there, it's messing with the bonds at this place here.
Here, the bonds just go along, they go along.
And then all of a sudden, I've got a misregistry now because of that dislocation-- because of that dislocation.
One way to look at it is with the model.
Another way is just get ears of corn.
I did this last night.
I actually-- I got ears of corn.
That's really true.
And I looked inside.
This isn't from there.
This is from the internet.
But there it is.
The corn needed to grow another row and so-- it's not going to grow a half kernel.
Well, actually, it could.
It does sometimes.
But here, it grew another full row of kernels.
And there it is.
There's a dislocation.
It's very similar to what we're looking at.
Now, there are two types of dislocations.
This one, where you insert an extra plane in this way is called an edge dislocation.
There's another type of dislocation that we won't talk about in this class called the screw dislocation.
You can look it up.
It's a different type of line defect.
But the one that we're concerned with is called an edge dislocation and it's described exactly in this way.
And the way you note it in an atomic scale drawing like this-- by putting that upside down T where the edge is.
An edge dislocation.
Edge dislocations in corn.
Now, you can actually see these things.
And on these models, the dislocations look very nice and uniform and you can hold it and look at it.
But in reality, here's an actual video of dislocations.
These are groups of dislocations.
Notice, these are 1D line defects.
They're places where you've got this extra plane.
Notice, that they're all over the place.
They're not just straight, they bend around in the crystal and they move.
And the movement is critical.
The movement is critical.
That's what's going to get us back to this, the movement.
This is the defect, and then the movement is what gets us this.
So let's take a look.
So here's an here's an example.
This is a piece of material that under the microscope is being pulled.
Watch what happens.
Well, those things are moving.
They're forming, they're ending, they're reforming, they're interacting with each other.
That one didn't, but whatever.
And they're spreading out, they're growing.
Those dislocations and their movement is why this doesn't crack.
It's why this can move, this can bend.
It's why this point is 100 times lower than you might have thought.
And that can be understood by thinking about the bonds.
That can be understood by thinking about the bonds.
Here's a sequence of pictures.
So this is the dislocation.
You see it there.
Now, what I'm doing is, I'm pushing-- or let's not push yet.
We'll do that on the next slide.
For now, I'm just watching it move.
Here you see it moving.
There it is.
How does it move?
Well, here's a model.
There is a dislocation and you can see that if I take this bonding area around here and I connect this atom to there and then you start pushing-- there's a strain field around there-- and then you push it over, you might be able to move it over to there.
And maybe you could keep on doing that and keep on moving it over and over until it gets all the way to that end-- all the way to the end of the material.
Here is a super polished, high detail animation of that process.
Here it is.
I'm starting over here and watch the dislocation.
There it is.
There it is!
And it's moving and it's moving, and those bonds are breaking.
Let's watch that again.
Here it is.
There, it formed.
But why did it form?
Because, you see, what happened is, I took this material and I applied a force to it.
I went back to the wire and I did this or maybe I did this.
And the material said, OK, hold on, how can I respond to this thing?
Well, either I can respond elastically and all my bonds could stretch, but I'm getting to this uncomfortable place here.
Or a dislocation could come in and allow me to translate a whole set of bonds over by one.
So I'm applying a force to this material.
You can think about it as a force maybe on the bottom g-- here, let's watch what happens.
Look at this.
I've got a little extra room here.
Now watch what happens.
There it is, there it is.
And I have moved the whole top row of atoms over-- the whole top three rows over by one.
So I have transformed this so that the force-- if you think about it, the force on the bottom could be applied that way and the force on the top that way.
The atoms get to a certain point where it's like, no, my elasticnesss-- I'm not sure I want to go anymore.
But a dislocation comes in and saves the day and it allows that to happen.
Because here's the alternative.
if I want that same translation to happen, that same slip, I would have had to break all the bonds at once.
If I didn't have a dislocation, this is what would-- ah, there's the dislocation.
One bond at a time, one bond at a time.
Or the much, much harder ask, especially since there's 10 to the 20 something of these, is to break them all at once.
There it is.
Bam.
That's why that doesn't happen.
It just takes too much energy.
But if I can just call up a dislocation to the rescue, I can translate an entire set of atoms with much, much, much less energy.
Did you see that?
So the dislocation moving is what allows plastic deformation, it's what allows these atoms to slide over one another.
It is what enables this region to be there and it's what defines it.
A very important point here-- aw, you got a goody bag.
That's OK.
Was he in the class?
It doesn't matter.
We share.
[LAUGHTER]
If you guys have friends-- just came in and took one.
If you guys have friends that need goody bags, we are here to help.
I will never turn down a goody bag.
There is a plane here that's moving on another plane.
There is a plane that's moving on another plane and it's doing it only because of this location, that one dimensional defect.
Now, that is slipping, so it's called a slip plane.
It's called a slip plane.
And it's the plane along which the dislocation moves.
[PHONE RINGING]
OK.
We got a phone going on there.
Now, I want to make a really important point here.
Because what the dislocation is allowing, what this defect is allowing you to do is resolve forces.
That's what you're doing.
I'm putting this force on-- it's again, the Instron.
I'm pulling the wire and the material is like, hold on, I got to respond to this.
How can I do-- yeah?
[INAUDIBLE]
Yes.
And I will come back to that.
It's this plane.
Where's the model?
Who's got the model?
Is that the dislocation model?
It's the plane where the dislocation comes in and can move.
Why?
Because that's the plane that is-- by motion of the dislocation, that's the plane that's slipping along another one by exactly this animation.
I'll talk about this slip plane in a minute also and more about it.
So what this motion, what this slip plane, what these movements of the planes allow is is it allows you to resolve an applied force.
So I come at this material with a force and I resolve it.
It's resolved at the atomic level-- and I'll finish this-- at the atomic level along that slip plane.
That's what it does.
The Instron pulls or I pull on the parachute, like the logo, and then either the material is going to break or maybe it's just in that elastic region and then it will go all the way back or it's going to deform.
And if it deforms, what's it doing?
It's feeling the force and it's trying to resolve it.
And it resolves it by those dislocations moving.
The planes move on top of each other.
Well, so let's go back to this plane.
What plane is it?
If I look at the planes, which are somewhere out there-- you can imagine that if I've got all those planes and they're looking at the Instron and the force being applied to me, which one is going to do the slipping?
Well, you can imagine this with a very simple analogy.
If I push on something-- if I push on a rope, what does it do?
Well, it kind of curls up, it doesn't do too much-- it doesn't move.
But if I really want to try to resolve force, I got to move those atoms.
But if I push on a stick and not a rope, then the stick just all moves.
So the plane that is going to move across another plane is going to be the most dense-- the closest packed.
It's going to be the closest packed.
So the slip plane-- let's write it here.
Slip plane-- and I'll give you an example in a minute.
Slip plane, closest packed or highest planar density.
Because then I'm pushing on the stick.
In the material, I've got stick and ropes defined by the plane.
You can see it over there.
Some of those planes, they're beautiful-- the yellow one, but it doesn't have that many atoms per area.
So if I try to move that one, it's not as strong of a plane to move and to resolve my forces at the atomic scale with.
So I'm always going to go for that strongest plane.
So that's a slip plane.
Now, a great analogy for this is the rug.
So if you're helping people move or you're setting up your own rug, and you get it and you put down the rug base like that, and then you put it down, and you're, ah!
I missed it by a foot.
I got it wrong.
This rug weighs-- rugs are really heavy.
You pick it up, you're like, oh, I'll just move it.
You call a friend and you both pick it up, and you're like, this is 1,000 pounds.
Who knew?
It's really a pain.
And so then you think about dislocations and you think about how a material would handle this situation.
And you say, well, if I just make a little dislocation, like a little crinkle there, and I move that, think about how much effort it takes to move that instead.
Not much.
You make a little crinkle, and then you move it, and then you move it.
It doesn't take much force to do that.
It takes a lot less than picking up the whole rug.
That's the motion of a dislocation.
We just talked about the plane that it is, but which direction?
Which way should you move it?
And so this is the second part.
So you have the slip plane, the closest packed or highest planar density, and then you also have the slip direction.
The slip direction is the other part.
Which way does it go?
I've got the closest packed plane.
Which way should it go?
Well, for this, you can see from the experiments, and when you look at the wire-- again, if I take a copper wire and I pull it and I look at it with my eyes, it just looks like the uniform wire's been stretched.
But now I magnify it.
This is what you see.
So you can see that there are very definite directions.
This is actually all the same direction.
So that's a slip plane and there's a direction that it slides.
I think this can be understood-- I love this picture, because I love ping pong.
These are ping pong balls and you guys can do these experiments yourself.
You put a bunch of ping pong balls in a row, and then measure the force that it takes to slide it depending on whether they're closely packed or not.
This is a little counterintuitive sometimes when you first see it, but it makes sense.
The more densely packed the plane is, the easier it is for one set of atoms to slide across the other.
The easier it is.
So you can feel it.
If I have to let this one-- and they showed it just by angle at which it would slide or roll.
I like the idea of two people going in there-- and here, you'd have to apply more force to make that one slide than this one.
You can see it, again, with this super precise animation.
There it is.
One of them and there's the other one.
Look at how much more work you got to do to get that thing to go over and over.
No.
If you've got a high density of atoms, it's actually easier to slide.
It's easier to slide because you've got more bonds.
And so I'm not having to fully break a bond before I get to the next one.
So the slip direction then is going to be the highest density direction, so it's also the close-packed-- I've got an example there-- close-packed direction.
So notice, this would be like a direction-- a vector and this is a plane.
Well, that's jogging some memories of understanding crystals by their Miller planes and directions.
We say, well, what would this be for, say, FCC?
There's an FCC crystal and there's an FCC lattice.
So if I had, say, FCC as an example-- well, OK, so let's see if I can really quickly-- oh, boy, here we go.
There it is.
And here are the face atoms.
There we go.
OK.
That's the outer part of FCC-- three of the faces.
And now, OK, but if I take a 100 plane-- so let's take the 100 plane.
Then I've got that.
And you'll remember, I've got these atoms on the corner.
Why did I draw that so much bigger?
Let's not do that.
That would be like the 100 plane.
And this one might be the usual lattice constant A. You could also look at the 110 plane.
Here it is.
The 110 plane.
That would look like this and this.
That would be the 110 This is just bringing back memories-- I know good ones.
Here is the 111 plane.
So here, we've got this one, this one, and this one.
In an FCC metal or crystal, which plane is going to slip and along which direction?
You can get that now.
Because you can calculate the planar densities.
In which case is the packing of atoms-- in which of these planes is it the highest?
Well, you've got to know the number of atoms.
So how many atoms are in this?
2.
How many atoms are in this?
Oh, why?
1/4, 1/4-- I'm just counting in the unit cell of the plane.
So 1/4, 1/4, 1/4, 1/4-- 1.
It only counts in the plane if the plane goes right through the atom.
So here in the 110 I've got 1/4, 1/4, 1/4, 1/4.
OK.
That's 1, plus 1/2, 1/2.
Two.
I've got two atoms in that plane-- effectively, two atoms in that plane.
But what about here?
Oh, boy.
OK.
1/6, 1/6, 1/6.
You see it from the geometry it's a triangle.
So that's 1/2 from those corners, plus 1/2, 1/2, 1/2.
2.
I've got the same number of atoms in those planes of the unit cell-- of those planes drawn within these unit cell boxes.
But they're different planar densities.
They're different planar densities.
Because the area here is equal to a squared in this case, it's equal to root 2 a squared in this case.
So it's larger.
Same atoms, larger area.
That's not going to have a higher packing than that.
And now I get to have really a lot of fun with triangles and thinking about the height here and stuff like that.
And the area of this one is equal to root 3 over 2 a squared less than 1.
That's going to have the highest planar density.
You know it.
That's going to have the highest planar density.
So that's a connection now.
So you can connect now what we've learned about Miller planes, about crystallography to this simple calculations of density, to this incredibly important behavior of materials-- plastic deformation.
Because now you know how that's going to plastically deform.
It's going to deform along its closest packed plane.
And you can also look at the directions.
And it's shown here that the slip direction will be along one of those-- that's the highest density direction, the 110.
So it's going to slip along one of those directions.
Good.
Slip plane plus this together combined-- these are called slip systems.
The slip plane and the direction.
That's called the slip system.
OK.
Now, there's another thing that happens with this location that's so cool and so important to materials and to the things we want to do with materials.
It has to do with the fact that, like I said, the dislocations come in and they can be a total mess and entanglement.
By the way, how did it come in the first place?
If I started with a perfect crystal, where did it come from?
How could there be a dislocation?
It can come in from the edge.
You've got an edge there.
There can be a mismatch and I call it up-- I need a dislocation or I'm going to break.
Boom.
Comes in from the edge, comes in from the edge.
They come to the rescue.
This is a simulation of exactly that done by the chair of the Department of Civil Engineering, Marcus Beuhler-- a simulation he did some years ago.
But he's modeling the dislocations-- that's what you're going to see here-- as a piece of metal is cracked.
Watch this.
Watch them come in.
It's saying, I need you, help me.
And there they go.
Now, look at what happen-- there's so many of them forming and forming, and now tangling and tangling and tangling.
Then he's going to zoom in.
It's very cool.
Those are dislocations like we saw in the experiments, but this is a computer simulation of them.
They're still kind of tangling.
Here they go.
They come in, they get called in to relieve the atomic force and let the material slip.
But there's something that happens now.
There's something that happens.
Because now we go back to the rug-- we go back to the rug.
And look at what's happened.
I'm going along and I did the calculations and I had no one to lift it, it's too heavy.
But I'm going to create a little dislocation and move it along.
And I come across someone else's dislocation here.
Look at this.
I'm trying to roll mine and there's another one there.
What's going to happen?
I can't go anymore.
I'm blocked.
I'm blocked.
So when dislocations tangle up, you can imagine now it prevents dislocations from moving.
But dislocations moving is what gives me the plastic regime.
So as I introduce dislocations, I make it so that it's harder for dislocations to move.
There's actually a name for that.
There's a name for that because it really changes the mechanical properties.
It's called cold hardening or work hardening or strain hardening-- sorry, cold work.
Cold working.
So work hardening or sometimes strain hardening.
Why is it called hardening?
Because you're literally making this material harder.
What's happened is, I've taken away ductility, so I've made it more brittle.
I've taken away the plastic deformation.
It can't do as much plastic deformation, because that only happens by motion of dislocations and I'm locking them in.
But I'm letting it maybe go a little further in how much it can elastically deform.
Maybe now, once it gets to here, it says, you know what, I've got all these dislocations in there, It's not letting me plastically deform, so I'll keep elastically deforming.
But that gets you up to much higher stresses.
It gets you up to much higher stresses with elastic deformation.
And so this is a plot-- look at that.
That's called the-- oh, I should have put that down there.
Let me label that because it's a pretty important point.
I labeled the fracture point.
This is the yield point.
There it is, the yield strength.
That's called the yield because it's where it yields to plastic deformation.
So here you go.
You've got some steel, you've got some brass, and you've got some copper.
This is plotting-- look at that.
This is the percent cold work.
Cold work is work hardening.
Work hardening is adding dislocations on purpose-- on purpose.
So that what?
So that I increase the yield strength so that this material can elastically deform now up to higher and higher and higher strengths.
But the ductility goes down.
When you bend a paperclip, don't you go and tell anybody it's because of heat that it breaks.
That's not why a paperclip breaks.
It gets hot-- or warm.
You bend it back and forth, it breaks because you are putting dislocations into it and you're making it more brittle.
In fact, if you heated it up, you would anneal those out and make it more ductile again.
That's how you get rid of the dislocations-- you've got to heat it back up.
It makes it brittle, the ductility goes down.
Why does this matter?
Well, this is one reason.
If you don't plan your cold work carefully, you might make the material too brittle.
You wanted it to be so hard because this was such an important ship and it was going to be a big deal and the launch was really exciting.
And then it cracks in half, the entire ship.
Why?
Because you didn't look up what dislocations mean.
You didn't take 3.091, that's why.
That's a pretty big crack.
The main why this matters-- oh, I couldn't help it.
I am a big fan of wind.
Wind energy is growing and growing and it's such a great national resource.
Here's the global capacity.
This is install capacity for wind turbines.
But see, this is a mechanical materials problem that you are now equipped to think about more deeply.
Because, you see, you can do a lot of different experiments on those turbines.
So the blades here are critical.
You can imagine that you want them to be light, but if they're too light, they may not be strong enough.
And then how do they need to be strong?
Because you've got huge amounts of wind coming at them.
And it turns out, you need to hit just the right balance of elastic deformation before it goes into some plastic regime.
You need to hit just the right balance of ductility.
So here's, for example-- these are some simulations.
Here are some experiments on a new material for a wind turbine blade.
And then you put it out there and look at what happens-- ice.
By the way, this ice comes off at hundreds of miles an hour in chunks.
These farmers are not happy about that.
Seriously.
And those are bugs.
Actually, bugs in wind turbine blades is a serious problem.
How do you clean bugs off of it?
Because it dramatically changes the aerodynamics and the efficiency.
It also can damage the blade itself.
So there's all sorts of work going on.
How do you make bug-proof wind turbine blades?
OK.
Well, now just spray it with something.
Ah, but then does it have the right plastic deform-- does it have the right yield point or is it just going to crack?
And by the way, it's got to have 5 times 10 to the 9 cycles before it can fail.
That's the metric.
So that's a pretty big ask of a material.
It all comes down to understanding this curve.
And in the broader sense of materials, this to me is a very exciting ask.
Why?
Because if you look at a plot of the density of materials-- heavy, light.
Good.
Kilograms per meter cubed.
And the Young's modulus-- now, this is a measure of the strength of the material.
It's a measure of how much strain you could put on the material before it breaks or goes through deformation.
But look at this.
Different materials are here-- rubbers, foams.
OK, foams have relatively low Young's modulus, but they're really light.
That could be good.
Up here you've got metals and alloys, ceramics, you've got polymers in here.
But notice, I've got so many different applications and needs in the applications and I've got this plot where I've got nothing here and nothing here, even though, if I could fill this out and dial up any stress/strain curve for any density or Young's modulus, you can make a big difference in a lot of different applications.
So I think this is a great challenge.
Have a good night.
See you guys on Friday.