Flash and JavaScript are required for this feature.
Download the video from iTunes U or the Internet Archive.
Topics: Modeling of elasto-plastic and creep response II
- Strain formulas to model creep strains
- Assumption of creep strain hardening for varying stress situations
- Creep in multiaxial stress conditions, use of effective stress and effective creep strain
- Explicit and implicit integrations of stresses
- Selection of size of time step in stress integration
- Thermo-plasticity and creep, temperature-dependency of material constants
- Example analysis: Numerical uniaxial creep results
- Example analysis: Collapse analysis of a column with offset load
- Example analysis: Analysis of cylinder subjected to heat treatment
Instructor: Klaus-Jürgen Bathe
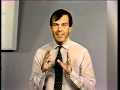
Lecture 18: Modeling of Ela...
Related Resources
Study Guide (PDF)
Readings
Sections 6.6.3, 6.6.4
References
Snyder, M. D., and K. J. Bathe. “A Solution Procedure for Thermo-Elastic-Plastic and Creep Problems.” Nuclear Engineering and Design 64 (March 1981): 49-80.
Rammerstorfer, F. G., et al. “On Thermo-Elastic-Plastic Analysis of Heat-Treatment Processes Including Creep and Phase Changes.” Computers & Structures 13 (October-December 1981): 771-779.
Kojic, M., and K. J. Bathe. “The 'Effective-Stress-Function' Algorithm for Thermo-Elasto-Plasticity and Creep.” International Journal for Numerical Methods in Engineering 24 (August 1987): 1509-1532.
Kojic, M., and K. J. Bathe. “Thermo-Elastic-Plastic and Creep Analysis of Shell Structures.” Computers & Structures 26 (1987): 135-143.
Eterovic, A. L., and K. J. Bathe. “A Hyperelastic-Based Large Strain Elasto-Plastic Constitutive Formulation with Combined Isotropic-Kinematic Hardening Using the Logarithmic Stress and Strain Measures.” International Journal for Numerical Methods in Engineering 30 (October 20, 1990): 1099-1114.
Montans, F. J., and K. J. Bathe. “Computational Issues in Large Strain Elasto-Plasticity: An Algorithm for Mixed Hardening and Plastic Spin.” International Journal for Numerical Methods in Engineering 63 (May 14, 2005): 159-196.
The following content is provided under a Creative Commons license. Your support will help MIT OpenCourseWare continue to offer high quality educational resources for free. To make a donation or view additional materials from hundreds of MIT courses, visit MIT OpenCourseWare at ocw.mit.edu.
PROFESSOR: Ladies and gentlemen, welcome to this lecture on nonlinear finite element analysis of solids and structures. In this lecture, I'd like to continue with our discussion of inelastic material descriptions we use in finite element analysis. Particularly, I'd like to now discuss with you creep, creep of materials.
We considered already in the earlier lecture that a typical creep law used in engineering practice very widely is the power creep law, shown here. Here we plot creep strains as a function of time, and curves that we would typically obtain using this creep law for constant stress values with time are shown here. Notice that as, of course, the stress value increases, which however is constant in time, we obtain a larger creep value.
Creep strains increase, the creep strains increase, in other words, as the stress increases clearly shown also by this law. Notice a1 and a2 of course, and a0 are constants that are determined from laboratory test results.
There are a number of other creep laws. Two are listed here. One here, shown, and another one shown here. Notice in this one here, the temperature, which affects creep strains quite heavily, enters explicitly right here. In the other creep laws, the first two ones, the one that you saw on the earlier view graph, and this one, these constants, of course, a0, a1, a2, and so on, would depend on the temperature. And if the temperature is constant, you would simply select them depending on that temperature condition, and model creep strains this way. However, as I pointed out, here temperature enters explicitly.
We will not discuss these creep laws further. The numerical computations with these creep laws are very similar to the numerical computations that we perform when using the power creep law. So I will now use the power creep law as an example to discuss.
The creep strain formula, given here once again, cannot directly be applied to varying stress situations because the stress history does not enter directly into the formula. Let us look at that much closer.
Here we have a very simplified example where we start off with a certain stress level, and then that stress level drops down to this stress level. Notice that if we were to apply the formula sort of "blindly," blindly in quotes, we would obtain creep strains that vary, depending on this stress level, as shown here. And then we might say suddenly the creep strain would drop down, and we would carry on going on this curve here. To creep curve, creep strain curve, that corresponds to this stress level.
Now, this is really quite unrealistic that suddenly when our stresses decrease, the creep strains decrease. Creep strains are accumulated along this curve here and they should certainly be staying right here. And the ensuing creep strain should, of course, now depend on the curve in which sigma 1 enter, but we should not see the sudden decrease in creep strain.
And we need to introduce the concept of strain hardening, the assumption of strain hardening. And this says the following. The material creep behavior depends only on the current stress level and the accumulated total creep strain. And we establish the ensuing creep strain by solving for an effective time.
Let's look at that closely. Here we have that at a particular time, the creep strain is given via this formula. Now, if we know the creep strain corresponding to a particular time, then we of course know the stress as well, and we know these constants. Then we can solve for what is called here an effective time. This effective time is not the physical time, it's a time that is simply used for the numerical solution.
So we solve for this tbar, and then knowing this tbar we can proceed with the creep calculations at a different stress level. Let's look how we would use that tbar. First, we would enter here. Now in this equation, knowing tbar, simply substitute into here, in terms of the creep strain that we are given from the previous history, and we now get a new creep strain rate. This is how we do the actual computation. Let's look at what this means pictorially.
Pictorially, we now look again at the situation where we have a certain stress value, and that stress value drops down, say, to here with time. As long as we are having this stress, our creep strain accumulates as shown here. As soon as this stress drops down, we are going over to this curve. So there's no sudden decrease in creep strain, say down here, down to here and then increase in creep strain, the way we looked at it earlier. Instead we continuously increase the creep strain. Let's look at how do we get this curve here.
Well we talked about the evaluation of tbar. tbar is an effective time. With this creep strain given at the time that this stress value drops down to here, with this creep strain value given, we enter into the formula corresponding to this creep strain accumulation and calculate tbar. tbar, the effective time, would be this value right here. We use now this formula, shown by this black line here, to calculate the corresponding increase in creep strain, corresponding to this level of stress.
This means that if I draw a little triangle in here, that this line here, for example, is equal to that line. And this slope, or this distance here is equal to that distance. In other words, I can mark this as, say, a and b, and I have here a and b as well. So basically, we are translating this curve here to right there. And that is shown by these blue arrows.
Notice all of this is achieved by the evaluation of the effective time. The effective time corresponding to this creep strain, and this effective time is applied to the creep strain accumulation formula corresponding to this sigma 1 stress level.
Well the increase in stress is modeled similarly. Here we have initially stress sigma 1, and suddenly an increase to sigma 2 level. We would follow this curve here, corresponding to sigma 1. And now the increase in stress is captured by solving for the effective time. Using this level of creep strain, we enter into the curve, shown here in black, to obtain the effective time corresponding to this curve here. This is the curve, of course, corresponding to this sigma 2 level. And we translate these points over, as shown by the blue arrows, to obtain this material response curve.
So we are now using the effective time again to evaluate the ensuing creep strain when we are going from sigma 1 stress level to sigma 2 stress level. If we have cyclic conditions, we proceed similarly. Here, we have first sigma 1, and then as stress reverses to sigma 2. Notice sigma 1 brings us along this curve, and at this particular time, we now reverse the stress. And here we have to be careful to recognize that this curve here, which I'm showing now in green, corresponds to that curve there.
In other words, as I proceed along this curve here, I would proceed along that curve there. The reversal in stress is picked up by saying that the accumulated creep strain in one direction corresponding to sigma 1 tensile stress is sort of, say, forgotten, and you simply take this curve here to be the reflection of that curve.
So this is the condition or the modeling of cyclic loading conditions as regards to creep strain. Of course, these were now the one dimensional situation, and in a multiaxial stress state, we have to generalize these considerations to the multiaxial conditions. Let's look at the multiaxial creep, how we proceed there. Here we have the stress at time t plus theta t is equal to the stress at time t plus an integration of the stress strain law times the elastic strain here, differential elastic strain increment-- this is the elastic stress strain law-- from time t to time t plus theta t.
If this matrix is constant, we can, of course, pull it outside the integration sign. The stress strain integration is performed for the multiaxial stress state using the concepts that we discussed for the uniaxial stress state and generalizing them to the multiaxial stress state.
We defined for this purpose an effective stress shown here. These are deviatoric stresses that we already encountered in the discussion of plasticity. An effective strain, shown here, and we use now these two quantities in this material law, the power material law. We only consider now the situation of stresses monotonically increasing or being constant.
We do not go into depth regarding cyclic loading conditions because we don't have really time to do so. The assumption that the creep strain rate are proportional to the current deviatoric stresses is giving this equation, and that equation is very similar to what we have seen in von Mises plasticity where gamma is given down here.
Notice that the effective creep strain rate is given via formula where the effective time goes in here. This is the effective time calculated much the same way [UNINTELLIGIBLE PHRASE] in the way that I discussed earlier for the uniaxial conditions. Except that we have to now deal with the effective stress here in the effective quantities on the creep strain as well. In other words, we calculate this effective time just the same way as we did it in uniaxial conditions, but always using effective stress and effective strain quantities.
Using matrix notation we can then write that the creep strain increment, the differential creep strain increment, is given via this right-hand side. D is an operator shown here for 3D analysis that gives us the deviatoric stresses from the actual stresses. In the analysis of creep problems we perform a time integration, and this time integration can be difficult due to the high exponent on the stress. In fact, solution stability arise if we, for example, use the Euler forward integration with too large a time step.
A rule of thumb is given here where we want to allow only that the effective creep strain increment is smaller, equal to 1/10 of the current at time t, effective elastic strain. This is a very good rule of thumb, however, it can be conservative. In some cases, you can really increase this coefficient quite a bit.
Alternatively, we can use implicit integration in which when we use the alpha method, we use this formula here. And we would use an implicit integration typically alpha greater equal to 1/2. Alpha can, in this formula, vary between 0 and 1. Of course, when alpha is equal to 0, we simply have the Euler forward method.
Let's look at how we would use this formula when alpha is greater, equal to 1/2. We would calculate the stresses corresponding to the i minus first iteration. And here we have to pause a minute to remember to recall that this i minus first iteration is the iteration that we have been talking about in earlier lectures when we iterate for the equilibrium of R equal F. Or we are evaluating in each iteration k times theta U is equal to theta R, and the theta U carries the i superscript, and the theta R carries the i minus 1 superscript. Remember, we talked about the iteration for nodal point equilibrium of external forces with nodal point forces that are corresponding to the internal element stresses. That i minus 1 up here refers to that iteration.
This k down here refers to the iteration that is an addition necessary at each integration point level due to the fact that we use an implicit scheme. Well this left-hand side is calculated by taking the stress at time t, which we know already, and adding to it an increment in stress obtained via the elastic material law here.
The total strain increment from time t to time t plus theta t, iteration i minus 1. This i minus 1 corresponds to that i minus 1. We know this value, of course. Minus the creep strain calculated based on the stress at the end of iteration k minus 1. That one goes right in here. It goes in there as well. And therefore, these are the creep strains corresponding to the end of iteration k minus 1. We calculate it right inside and obtain an updated value of stress corresponding to iteration k.
This is the iteration that has to be performed at every one of the integration points in the finite element mesh. Here we show nine-node element with 3 by 3 integration. So is the kind of iteration that has to be performed at every one of these integration point stations.
When alpha is greater or equal to 1/2, we obtain a stable integration algorithm. This is a statement arrived at from a linearized stability analysis, so in practice we use frequently alpha equal to 1. Also, to accelerate this iteration at the integration point level, it is frequently effective to use some form of Newton-Raphson iteration.
The choice of the time step using the implicit integration scheme is now governed by two considerations. The first one, of course, you want to converge in the iteration, which had the iteration counter k minus 1 to k you want to converge in there. And of course also, even if we do converge, we want to have an accurate integration. Our errors in the integration should not be too large.
Of course, we can also use some form of subincrementation, the way we have been discussing it when we talked in the last lecture about plasticity. If we compare time steps that are usable, that are realistically usable with the implicit scheme with alpha greater/equal to 1/2 with the time step that we are bound to use when we use alpha equal to 0. Because we need to have a time step small enough to have stability of the integration. We find that with alpha greater/equal to 1/2, we can use usually, frequently, much larger time steps. But not always. We will see later on in example where alpha equal 0 performs just as well as the scheme of alpha equal to 1/2.
If we deal with thermoplasticity and creep, we have to model the plastic strain components, and here we have schematically shown how we can model those strain components. Notice for different temperatures, for different temperature levels, we have different stress strain laws. In each case, we have assumed the bilinear assumption. Notice that the yield stress drops down as the temperature increases, of course. And with increase in temperature, our creep curves looks this way. Notice that our creep strain, of course, increases at a given stress when the temperature increases.
To evaluate the stresses in thermoplastic and creep analysis we use this equation here. Notice elastic stress strain law. Of course, now changing with time, with temperature that is. And here we have the elastic differential strain increment. Thermal strain also enter now here as well. Creep strain, plastic strain, total differential strain increment.
If we use the alpha method, this integration without subincrementation, or, say, a subincrement of 1, going from t plus theta t in one step, we would have that this equation reduces directly to that equation. Notice this is here now the stress strain law. At time t plus theta t, temperature corresponding to that time would go in here. And here we have the total strain increment from time t to t plus theta t.
We subtract the plastic strain increment over the time increment, the creep strain increment over the time increment and thermal strain increment. And these are here, the corresponding quantities, total strain plastic strain, creep strain, thermal strain corresponding to time t.
Notice that ep and ec and e thermal have to be evaluated in this integration, and we evaluate them as shown here. Notice here, t plus alpha theta t sigma goes in. And if alpha is equal to greater/equal 1/2, typically we would use alpha 1/2 or alpha equals 1. For an implicit integration, we need, again, to integrate at each integration point to satisfy the stress strain equation.
Of course, t alpha is a coefficient of thermal expansion at time t. Please don't confuse this value with the alpha integration parameter that we talked about earlier.
The final iterative equation, if we use alpha greater/equal to 1/2 we would find looks this way. Stress strain law at time t plus theta t-- elastic stress strain law, I should say-- goes in here, and on the right-hand side, we have the total strain corresponding to time t plus theta t, iteration i minus 1. End of iteration i minus 1, plastic strain, creep strain, thermal strain, which are given corresponding to time t. And we subtract here the plastic strain increment, the creep straining increment, both based on the stress at the end of iteration k minus 1. And of course, the thermal strain increment.
So this is the equation that we would solve at each integration point, at each integration point in the finite element mesh by iterating until convergence is reached. Until, in other words, this stress here is basically equal to that stress. And as I pointed out earlier, we really need to use some form of Newton-Raphson iteration in order to accelerate this iteration when theta t is not-- unless theta t is very, very small.
Of course, we can also use subincrementation. And then the convergence will be increased because our time step over the subincrement is smaller. But I should also mention, as I did already earlier, it is very effective frequently to use this new algorithm, the effective stress function algorithm, to solve basically this equation. And please look at the reference given in the study guide if you're interested in reading up about that method.
Let's look now at some example solutions. And the first problem that I'd like to discuss with you is a very simple problem of a bar under a uniaxial stress sigma. The creep law that we want to use is given here. The stress is method in megapascal, time in hours, and E and nu, the elasticity constants are given down here. What we want to do here is to look at various solutions that have been obtained with alpha equals 0. We don't use subimplementation. Alpha equals 1. The effective stress function procedure was used here.
In all cases, we assume an MNO formulation, or we use an MNO formulation. And we use Full-Newton iteration without line searches, with these tolerances, and we discussed the meaning of these tolerances in an earlier lecture.
In the response predictions for which we used the ADINA program, of course, you will be seeing the elastic strain plus the creep strain. Let's first look at the response when we put a constant load of 100 MPa onto the specimen when the creep material law is shown here, or with this material creep law. Notice that displacements are measured upwards, time measured horizontally here. And the time step that we used in this particular case was 10 hours with alpha equal to 1.
So this is the total strain accumulation, but measured in terms of displacement. Of course, the bar is 5 meters long, so you could directly obtain the strain by simply taking this displacement divided by 5.
If we increase the stress from 100 MPa to 200 MPa, you obtain this response curve for the displacement at the right end of the bar. We use, again, the alpha equals 1 parameter with the effective stress function algorithm, and a time step of 10 hours.
In this particular case, we had a change from 100 MPa to 200 MPa in the applied stress, and that is modeled as shown on this view graph, constant stress up to time 500 hours. And then the stress increment taken over 10 hours. And then the stress is constant at 200 MPa.
Stress reversal from 100 MPa to minus 100 MPa gives this response. Notice we are not crossing exactly at that point because of elastic strains. A constant load of 100 MPa, but now with a different exponent on the time for the creep law gives this response. Theta t 10 hours, alpha equals 1 still. If we increase the stress from 100 to 200 MPa with this new creep law, or new exponent I should say, you get this response for the displacement at the right end of the bar. And finally, the stress reversal from 100 to minus 100 MPa gives this response. Notice we have here, of course, a or a displacement at the end of the bar due to the elastic effects.
Let's consider now, the use of alpha equals 0 for the stress increase from 100 Mpa to 200 MPa problem, and see how our alpha equals theta solution performs when compared to alpha equals 1. You can see that with theta t equals 10 hours, we get a response that is very much the same of the two responses calculated with alpha equals 0, and alpha equals 1/2-- very close to each other.
If you use a lot of time steps, theta t equals 50 hours, both algorithms converge, but the solution becomes less accurate with alpha equals 0 in this particular problem, in this particular problem. Notice our baseline solution that we are comparing with here corresponds to alpha equals 1 and theta t equals 10, which is a solid line.
When we take and even larger time step, theta t equals 100 hours, we find that alpha equals 0 does not converge anymore at t equals 600 hours. Whereas the use of alpha equals 1 gives very good results. Alpha equals 1 gives these triangles here, and they lie exactly on the response obtained with alpha equals 1 theta t equals 10 hours. So excellent results with alpha equals 1, even when the time step is 10 times larger. With alpha equals 0, we could only obtain the response up to this point, and then we did not converge anymore in the solution.
This was a very simple problem, but a demonstrative problem. Let us look at another problem now, another example, that has a bit more complexity, and I think that you also will enjoy looking at.
Here we have a column subjected to a compressive load, R, which is not applied exactly at the center of the column, but is applied with an offset. We analyzed this column as a plane stress problem. The material constant, elastic material constants are given here. In elastic buckling load, calculate it using analytical formulas. The Euler buckling load is given here as 4,100 kilonewton.
The goal of the analysis is to determine the collapse response using different material assumptions. First of all, is using an elastic material assumption. Then, assuming elasto-plasticity, and finally, assuming creep in the material. We use in each case the total Lagrangian formulation. If you were to try to use a material [UNINTELLIGIBLE] your only formulation for this problem, of course, you would never predict the actual collapse of the column. You have to include large displacement, large rotation effect. All of the assumption of small strain is quite reasonable even for this problem.
The solution procedure that we use will be the full Newton method without line searches. And these are the tolerance values that we're using, which we discussed already in an earlier lecture. The mesh used is a 10 eight-node quadrilateral element mesh. Here you see the eight-node elements, 10 of them. We don't show the nodes. But for each of these elements we use also 3 by 3 Gauss integrations. So notice through the thickness of the total column, we would have six integration point stations.
First we predict the elastic response. And in the elastic response using the total Lagrangian formulation, we enter with this stress strain law. Second Piola-Kirchhoff stresses are related to the greener ground strains via the elasticity constants, and we discussed this stress strain law quite a bit in an earlier lecture.
The response predicted is shown here. Applied force in kilonewton, and here the lateral displacement at the top of the column. Notice the Euler buckling load, calculated from classical analysis, is shown by the blue line here, and our analysis yield this response.
If we perform the elasto-plastic analysis with a strain hardening model is equal to 0. In other words, we assume perfect plasticity, a yield stress of 3,000 kilopascal. And we use it for von Mises yield criterion. In this formula, we would predict with this formula here, quite adequately, the large displacement elastic-plastic response, and of course, this will be for this column, the large displacement collapse response.
Notice that CEP 0 is the incremental elasto-plastic constitutive matrix calculated the way we discussed it in the previous lecture. But instead of using the engineering stresses, we enter now with the components of the second Piola-Kirchhoff stress, right in there.
The plastic buckling that is calculated using this approach is shown here. Notice this is the elasto-plastic response curve, applied force, lateral displacement at the top of the column. The elastic response curve is shown here.
Finally, we want to calculate the creep response. And for this analysis we have to select a creep law. This is the creep law that we selected. A power creep law with the exponent up here equal to 1. On the time, in other words, exponent from 1. Notice that we are entering here, of course, with effective quantities, effective creep strain, effective stresses, the way I discussed it earlier.
We do not include, in this analysis, plasticity effects. We apply in this particular analysis, a load, a constant load of 2,000 kilonewton to the column, and simply watch what happens to the column. Due to the creep strains, the displacement of the column will increase, and we want to measure, calculate the increase of the column displacement. And we say that the column has collapsed. This, of course, is somewhat arbitrary, but we say that it has collapsed when the lateral displacement at the top of the column is 2 meters.
This corresponds, by the way, to a strain of about 2% at the base of the column, and we know that our total Lagrangian formulation is quite applicable up to that percentage range.
We want to investigate varying time steps, and varying alpha. Alpha equals 0 is the Euler forward method, and alpha equals 0.5, and 1 corresponds, of course, to an implicit integration scheme.
If we do so, we obtain the collapse times given in this table. using theta t equals 0.5. With alpha equals 0 we get 100. With alpha equals 0.5, we get also 100. And with alpha equals 1, we get 98.5. So the collapse time predicted with theta t equals 0.5 is very close using any one of these integration schemes.
When the time step gets larger, the collapse time changes for alpha equals 0, for alpha 0.5, and for alpha 1. In fact, the difference between these collapse times for theta t equals 0.5 is quite a bit here, showing that this time step is a bit large for this analysis.
The column looks this way pictorially. At time 1 hour, the creep effects are still negligible. At time 50 hours, well there we have some creep effects already. And at 100 hours, collapse occurs of the column. In other words, the column displacement being two meters or larger at the top. In this particular analysis, we used theta t equals 0.5 hours, and alpha equals 1/2.
If we compare once more the different responses predicted, we find that with theta t equals 0.5 hours, the lateral displacement as a function of time predicted using alpha 1, alpha 0, alpha equals 0.5 as shown, as given here by these curves, and notice these curves are very close to each other. If we use the large time step, theta t equals 5 hours, we can see here that alpha equals 0, the alpha equals 0 curve is very close to the alpha equals 0.5 curve. Where the alpha equals 1 curve is quite a bit away.
So in this particular case, we really have a much larger area accumulation when we use alpha equals 1, than we have with alpha equals 0.5 or alpha equals 0. We conclude then for this problem that as the time step is reduced, the collapse times predicted using alpha equals 0, alpha 1/2, and alpha 1 are very, very close to each other. In fact, for theta t equals 2.5, the difference in the collapse times is less than two hours using the three integration schemes.
And we also notice that for a reasonable time step, in this particular problem, we certainly did not encounter any solution instability, particularly with respect to the alpha equals 0 integration method where one might have instabilities, as I pointed out earlier. For this problem, we did not encounter any such instability.
This concludes then what I wanted to share with you in terms of experiences as documented on the view graph. I'd like to now share some further experiences with you regarding an interesting analysis that we performed some time ago regarding a heat treatment process. And that analysis is documented on the slides, so let me walk over here and discuss these sides with you.
Here we have a cylinder, and it is this cylinder that is subjected to heat treatment process, namely initially the cylinder is at 900 degrees Celsius, and it suddenly cooled down to 20 degrees Celsius.
The objective of the analysis was first of all, to predict the temperature distributions in the cylinder as a function of time, as the cylinder cools down. And then to predict the corresponding stresses in the cylinder, and most importantly, to predict the finer, the residual stresses.
Here, once again, the cylinder. Here, the finite element model. Notice that we modeled one typical section through the cylinder, and that section is shown here. The center line of the cylinder is here, and we perform an axisymmetric analysis. Notice that we have a higher density of elements at the outer face or near the outer face of the cylinder than at the inside of the cylinder.
So then now because we are predicting higher temperature gradients, stress gradients at this end, notice that in this particular analysis, we constrain the top face to move just vertically up to basically remain a straight line. That was achieved using constraint equations. Of course, all these nodes along the top face can move over.
The assumption of this top face to move only vertically up is due to the fact that the cylinder will reflect the fact that the cylinder is assumed to be infinitely long.
The next slide now shows the material properties used for the temperature analysis. Here we have the heat capacity as a function of temperature. And here we have the conductivity as a function of temperature. This data was entered in the heat transfer analysis in which we wanted to predict the temperature.
These material properties here, Young's modulus, a strain hardening modulus, Poisson's ratio are entered in the stress analysis. Notice the large variation in Et, Poisson ratio, and E as a function of time over the range from 0 degree Celsius to 900 degrees Celsius.
Next we see the variation of the yield stress as a function of time. Notice very marked variation. And notice this here is a region of a face change where we have a tremendous drop in the use stress.
The next slide now shows the coefficient of thermal expansion as a function of temperature. Notice that the coefficient is positive in this regime and that regime, and is negative here to take into account the face change effects.
On the next slide now we see the prediction of the temperature as calculated. Notice initially, the whole cylinder is at 900 degrees Celsius. We measure here the axes along the axis of the cylinder. And here, temperature. And as time progresses, the temperature changes down to 20 degrees Celsius at 300 seconds.
Let's look a little bit more closely here. Notice at point 0.05 seconds, this here is the temperature distribution in the cylinder. At 0.5 seconds, this is the temperature distribution in the cylinder. And at 3.5 seconds, we see this temperature distribution. At 18.5 seconds, we see this temperature distribution. Notice the last temperature gradient right here in this area, and this is the area where we had a denser finite element mesh. Then close to the center line of the cylinder.
The next slide now shows the temperature as a function of time, here time, here temperature at a number of locations. First of all, at the axes of the cylinder, and notice there we have a calculated curve, the solid curve, and a measured curve, the dash curve. They are remarkably close to each other.
This is here the calculated temperature at element 14 within the cylinder. And this is here the surface temperature , calculated because there we did not have any measurement. The only measurement that we had to compare with was the temperature at the axes of the cylinder. Notice that at 300 seconds, the axes, as well as the surface, basically all points in the cylinder have reached 20 degrees Celsius.
The next slide now shows the results obtained in the laboratory regarding the residual stress field. Here we see as a functional of the radius through the cylinder, the residual stresses, circumferential stress, sigma phi phi, longitudinal stress, sigma zz, and radius stress, sigma rr, once again, as obtained in the laboratory. We wanted to compare our calculated results obtained with the finite element solution with these laboratory results.
And the next slide shows the results obtained in the finite element analysis. Sigma phi phi, sigma zz, and sigma rr. And if you compare these results with the results obtained in the laboratory, you see a very close correspondence. In fact, an excellent correspondence for this very complex problem that is considered here.
Notice that we are making various assumptions on the material model level. In other words, a bilinear material assumption, et cetera, et cetera, for this analysis. If you are interested in the details, please refer to the paper in which we are describing this analysis in much more depth, and the references given in the study guide.
This then brings me to the end of what I wanted to discuss with you in this lecture. At closing I like to really mention to you that we have, in these two lectures in which we discussed elasto-plasticity and creep response as modeled in finite element analysis, we have in these two lectures really covered only quite a bit of the material that is worthwhile looking at, and studying, and getting familiar with.
The elasto-plasticity and creep response of structures is, of course, a very large field, and we have just taken two lectures to cover some of the aspects as we use them in finite element analysis. There's a lot more we could talk about. But thank you for your attention.