Flash and JavaScript are required for this feature.
Download the video from Internet Archive.
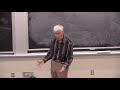
Lecture 22: Workforce Planning
The following content is provided under a Creative Commons license. Your support will help MIT OpenCourseWare continue to offer high quality educational resources for free. To make a donation or to view additional materials from hundreds of MIT courses, visit MIT OpenCourseWare at ocw.mit.edu.
GABRIEL SANCHEZ-MARTINEZ: So today's topic is workforce planning. And we have Professor Nigel Wilson, who is the father of the Transit Lab here at MIT and of this course. He's sort of the master of everything related to transit and the applications of transit data, to operations planning and study.
You may remember that we divided the course into themes. And so we already talked about crew scheduling in the context of operations planning.
And now we're in the strategy and policy theme. So this lecture is on looking, again, at proofs and planning, but from a strategic perspective. I think that's probably--
NIGEL HM WILSON: That's great.
GABRIEL SANCHEZ-MARTINEZ: --enough of an introduction. Maybe you can provide--
NIGEL HM WILSON: Yeah.
GABRIEL SANCHEZ-MARTINEZ: --a little more.
NIGEL HM WILSON: Thank you, Gabriel. It's good to see a fair number of familiar faces and some new ones I don't know yet. So I encourage you all to jump in and ask questions if I'm not making things clear or if you disagree or whatever. But I'm delighted to be here with you today.
So the work that I'm going to be discussing is work that I haven't done recently. It's about workforce planning. And it was done with the MBTA. Principally the results I'll give are for the MBTA as it existed 20-odd years ago. But the issues are exactly the same then as they are now.
In fact, I gave a summary of this presentation to Brian Shortsleeve and some of the other people at the MBTA a year and a half ago, or so. And they were thinking about maybe they really should [AUDIO OUT] --thing something like this again.
So what I want to discuss the problem in general of the approach that we've taken to this, and then look at three different levels of the problem. One is the strategic level, which is the long-term view, which fits in with Gabriel's statement about the theme of this part of the course being on strategy.
Then the tactical level, which is shorter range. And then the operational level, which is really short range. And these are all tightly connected and interrelated, as I hope I'll be able to explain to you.
OK, so the challenge that we have in this part of the operations planning process, if you think of it that way, is we want to provide good service. We've got hopefully a decent operating plan that we've developed and want to make sure that the service that's delivered is reliable. That requires decent equipment, decent infrastructure, and also a workforce that's motivated and there when you need them, which is pretty much every day.
So the operations plan you've all been through this at this stage in the course. So you know what goes into the operations plans.
So what comes out of the operations plan are a set of schedules, timetables, runs, or duties for operators to perform. And that require a certain amount of workforce or-- excuse me for using the term "manpower," but it's sort of the workforce that we need.
So if you don't have the right level of workforce available on a particular day or at a particular time on that day, then you've got a problem potentially. If you can buy work on an overtime basis, you can do that and at least not drop any trips.
That's going to cost you money though. And you may not be able to get the overtime, which will, again, produce unreliable service through dropped trips.
It may also, if some workers in the workforce feel that they can rely on overtime, which gives them a 50% premium rate, then maybe you can take more absence time. So there's a substitution relationship here between absence and overtime.
So if you rely more heavily on overtime, perhaps your absence rate will go up. That's not an outcome you want. So you've got to be very careful about that.
Certainly, if you can't buy the overtime and you don't have enough people on the property that particular day, that particular time, then you can drop trips because you don't have anyone to run the bus or to run the train. And that's a problem because that produces worse service reliability, worse customer satisfaction.
Politically, it's a very negative [AUDIO OUT] as well. And so workforce planning is actually a fairly critical piece of getting from the operations plan to good service on the street or on the rails.
This is sort of a high level view of what the problem is, as I see it. So on the left of this chart, you have the operator availability. So that means the number of drivers you have available on a particular day. That's affected by the number of operators you had available the previous day.
If you hired people, how many people are coming on to increase the supply? What sort of attrition-- what sort of outflow do you have in your workforce from your previous time, day, or time period? What's the absence?
Because those guys aren't going to be there. Those people aren't going to be there to deliver service. And of course, you have a roster, so everyone typically works five days and takes two days off. And that rotates among the workforce. So this is the supply side, in terms of the operator.
On the demand side, you have the scheduled service, which is a result of your operating plan-- what you want to provide. You have unscheduled service additions. And you potentially have unscheduled service deletions.
For instance, if there's a school vacation, you will drop some school trips-- trips which are primarily there on high frequency routes to provide school service. And these don't fit naturally into the timetable process because there's lot of overhead in developing and timetable, as I'm sure Gabriel has explained to you.
So you'll just take those trips off the table that day. And those operators are then available to provide other service that you need and to fill in for absent operators those days.
So you've got the supply. You've got the demand. And so you're down here looking at the availability versus the supply of drivers. I'll call them "drivers." The technical jargon in the industry is "operators."
In a perfect world, you'd have an exact balance between availability and demand, and you have no additional cost, and you've got someone to cover every trip. That will never happen.
Why? Because the operator availability is stochastic. It's uncertain. You don't know what the absence rate is going to be tomorrow. With the best will in the world, with the best models in the world, you don't know whether I'm going to be feeling well enough to work tomorrow.
So that's a problem. And for instance, in the MBTA, you don't know if you going to have a failure on the Red Line. You're going to have to bus parts of the Red Line tomorrow at 8 o'clock in the morning, OK.
So all of those uncertainties affect this balance between the availability and demand. So you'll never be here. I mean, statistically, it's virtually certain you'll never be there.
You're either going to be over here, where the availability is less than the demand. In that case, you have additional time costs, because you're going to have to try and buy operators to work that overtime. And perhaps more seriously, you have the risk of dropping trips if you can't persuade operators that they should work the overtime that day.
Or you're over here, where the availability is greater than the demand. In that case, you have additional personnel costs who aren't going to be used as productively as you might like. If they were going to be used productively, you'd have built them into the operating plan. So they're probably not going to be used as productively as your average operator.
So this is sort of one way of looking at the framework. We can think of, again, three levels of planning here. At the strategic level, this is typically looking at a one-year or even longer than one year horizon.
So it's not strategic in terms of infrastructure. It's strategic in terms of operations. So that's how many people will we need in the driver workforce over the next 12 months.
And how do we get a hiring plan that will give us the right number of people throughout the year? How do we allocate our vacations? Do we have a certain vacation liability?
If I'm a 20-year employee of the MBTA in the commons union, I probably have about five weeks vacation time over the year. So I get my five weeks.
But the MBTA management decisions include when to provide the vacation allocation. So you may have an overall life vacation liability of 2,000 vacation weeks. So the question of the strategic level, how do you allocate those 2,000 weeks of vacation liability over the course of the year?
And there are good ways of doing that. And there are bad ways of doing that. I mean, if you give vacation liability when people don't want to take vacations, what's likely to happen? Your absence rate's going to increase.
So you really want to give vacations when people want to take vacations. But you don't want to give them so much vacation when they want to take vacation that it really costs you a lot more money. In that case, maybe taking a higher absence will be a better way of dealing with that.
So there are really important questions on how to meet the vacation liability. And this is the timetable. We've decided what we need in terms of finding decent service.
And then, at the strategic level, I'd also include personnel policies. So as I think you all know, in many agencies, including the MBTA, you have a mix of part-timers and full-timers.
In the MBTA, you have Management Rights Act, which I'm sure you've heard about. Maybe Fred'll talk about that next week. It's a very interesting topic. And Fred will make a meal of it, I guarantee that.
So the MBTA management was given these rights by the legislature 35 years ago, 36 years ago. And so they cannot negotiate about not using part-timers. That's not part of the contract negotiation. That's a right they've been given legally. It's been challenged in the courts. It's been upheld.
And so they will use part-timers. They've decided to use part-timers in a way that I think is very unproductive. They use part-timers as apprentice full-timers. And so someone suffers through perhaps five years as a part-timer at the MBTA in order to reach nirvana of being a full-timer at the MBTA.
Well, that's one way of doing it. But I'm not sure that's the best way of doing it. Perhaps what you're doing is, you're making these part-timers suffer for five years, if that's how long it takes to get promoted from part-time to full-timer status. So they're sort of unhappy for that five years, because that's not what they want.
And it's pretty miserable working conditions. They don't get full benefits. And typically, they work a 6-hour day spread over 13 hours-- so covering the AM peak and the PM peak.
And they're doing nothing between the AM peak and PM peak. You hope they're not in bars. But they're certainly not doing anything productive with the property.
So that's the way the MBTA decides to use the management rights they were given by the legislature. I don't think that was a good decision.
If you have separate AM part-timers, might you be able to increase your workforce? I think so. You have people-- shop clerks who don't really start work until after the AM peak who might be very interested in supplementing their shop clerk job by having an AM-peak driving job.
And similarly, in the PM peak, you probably can increase your labor pool with people who are not interested in a full-time MBTA driver's job, but they would be interested in just a sort of a guaranteed, 3-hour piece of work every day.
So there are lots of different ways of implementing this. And I'm pretty sure the MBTA didn't do it optimally. So that's what I mean by personnel policies.
So all of these are at the strategic level. At the tactical level, what we're making decisions on is the time horizon is typically one timetable. How many timetables does the MBTA have per year?
AUDIENCE: Four.
NIGEL HM WILSON: Yeah, four. So you're making these decisions, running up to each timetable-- the start of each timetable period. And the main decisions are the staff. And you've sort of got your workforce fixed. And you're deciding how to allocate them across depots or garages or rail lines and by days of the week.
Those are the tactical-level decisions you're making. Those, it turns out, are actually quite important. If you make poor decisions, then you're going to be providing less reliable service or more expensive service than you otherwise would.
And then at the final level, your operational level, is here we are 4 o'clock on a Thursday. At 12 o'clock today-- so four hours ago-- the MBTA was deciding when to ask each extra board operator to show up for work tomorrow if they didn't have a guaranteed assignment. OK?
So there are unexpected absences that will occur tomorrow. You don't know when they're going to occur. You don't know whether it's going to be an AM report or a PM report or whatever it is.
And you have to make the decision about when, if you have five extra board operators that don't have an assignment, because a known, in advance absence, when you want them to show up? And that the daily report times for unassigned, extra staff is the operational-level decision.
Any questions about this, in terms of strategic, operational, tactical? And I'm not talking here about policies that may change-- absenteeism, for instance. Fred will talk about some of those next week when he talks about labor relations. But I'm talking about sort of a narrower piece of this puzzle. Any questions on this? Yes, Kenji?
AUDIENCE: [? Someone ?] become the part-time operator--
NIGEL HM WILSON: Yeah.
AUDIENCE: So are they required any license or--
NIGEL HM WILSON: Oh, yes. A commercial driver's license is required for them. But again, what I was saying is, you have choice about both who to recruit into those positions-- do we want an AM part-timer or a split-shift, full-day part-timer who's going to be unhappy until they get their full-time position at the MBTA that they really want. So yeah, sorry.
The other point I wanted to make is that how you select those people who will get promoted to full-timer. So you've decided, through attrition in the full-time ranks, you want to promote some part-timers.
How do you make that promotion? Do you promote based strictly on seniority? In other words, the first one to become a part-timer becomes the first one to be promoted to a full-timer?
Probably not, because you'd really like people who are motivated, who have a good absence record, a good accident record. So you'd like to use criteria in that promotion, which are more than just strict seniority.
And the MBTA, again, has been, I would say, not very effective in using that balance between seniority, which is an important issue-- you want to avoid favoritism and discrimination in the promotion process-- with having some elements of performance in the promotion process, I would argue. Did I answer your question?
AUDIENCE: Yeah.
NIGEL HM WILSON: Go ahead.
AUDIENCE: I was interested in the topic because, yeah, we have a similar culture for the station's time--
NIGEL HM WILSON: Yes.
AUDIENCE: --in Japan. But for the driver, they require a very strict license--
NIGEL HM WILSON: Right.
AUDIENCE: --which takes a long time to test. So we don't have any part-time drivers.
NIGEL HM WILSON: Right. Right, yes. And there are commercial driver's licenses required for the MBTA. A bus driver or train driver has to have a commercial driver's license. But it's not as a rigorous and long period of qualification as it is, I'm sure in JR-East. That would be my guess, anyway. Any other comments or questions? OK.
OK, so let's look at this as three levels of planning. So strategic level-- we're deciding the workforce size, vacation allocation over the year, and hiring patterns over the course of a year.
So by period of the year, the input into this includes absence hours. If we know we typically have more absence hours in the winter because the conditions are miserable-- you don't drive in snow and ice-- and if you have observed higher absence rates, that's important in making the right decisions on the strategic level.
Required extra work. If we know that we are going to be bussing on the Braintree branch of the Red Line because of reconstruction, then we'll build that into our workforce planning thing. So that's an example of required extra work. And attrition-- we do projections about the number of full-timers and part-timers who will be retiring or leaving the productive workforce over the next year.
On the right-hand side, we have input such as budget, the service plan, the operations plan, vacation liability-- how much vacation do we have to provide in the next year-- work rules and policies that we want to meet. And what I'm showing here is strategic level, tactical level, and operational level. And what you'll see is these downward arrows from strategy to tactics to operations, and the upward pointing arrows back up the chain from operations to tactical to strategic.
So let's explain each of these arrows. The downward arrows represent constraints on your decisions. So if you've made some strategic-level decisions on workforce size, that limits what you can do at the tactical level. And that's this downward arrow here.
Similarly, you make your tactical-level decisions at the beginning of a timetable, that limits what you can do at the operational level. These are these downward-pointing arrows between these boxes.
The upward pointing arrows are the relationships between that you need to know about how efficiently the operations level is conducted to make good decisions at the higher levels of the planning hierarchy.
So for instance, if you know that overtime is virtually impossible to get from your workforce, for whatever reason-- they may say, I'm just not going to cooperate, I'm not going to work, or that could be bad or good reasons for that-- then you need to know that in order to make the right decisions at the tactical level. And similarly, you need to know that to make the right decisions at the strategic level. So these are these upward-pointing arrows here.
And the difference in the inputs are just more detail. So absence hours by garage and by day of week is important input into the tactical level.
Absence hours by garage and time of day is important input into the operational level, OK. And you have work rules and policies as critical inputs on all these levels.
So this is a slightly different look at these relationships. And I want to lead you through this a little bit. So this is our strategic planning box where we're deciding workforce size.
What goes into this? The unit costs-- how much does it cost to provide a platform hour, which is an hour of driving a bus, by an overtime employee, a full-time employee, and a part-time employee? Those are very important, basic cost units that we need to have.
What's the budget, and what are the work rules? The work rules are important because they tell us how easy it will be to do certain things. And I'll give you an example of that later on. And of course, you have the scheduled hours, which comes out of your operations plan-- the timetable requirements.
So given that you've made a decision on the workforce size at the strategic level, on a particular day, you may have an amount of open work. What do I mean by open work? It's work that we want to deliver, but there's no one obvious to provide it. There's no one. So we'll try and buy time on an overtime basis.
So we're down here. And if we're lucky, the overtime-- there'll be someone available who's willing to work the overtime for increased pay. The negative side of that is it increases the strain on that employee who's working more hours than he or she was expecting to. That may produce this negative feedback on absence.
And I described it previously as the trade-off between how much do I have to work to get to a certain target income level? Well, that's one way of looking at it.
But the other way of looking at it, which is equally realistic, is if you're working harder, that puts more stress and strain on the body. You're more likely to be absent. Because there are two ways of looking at it, which both raise the concern about relying heavily on overtime and what that will do to absence.
Again, over here, if you can't get the overtime, you're going to be dropping trips. So reliability suffers. Negative effect on service reliability, service quality.
Presumably, that will affect ridership if it goes on long enough. And that will affect your operating plan, because your ridership's down. And so there's that feedback, as well. So this is sort of another way of looking at the framework.
Now let's look at the strategic level in terms of the planning process. What I've shown here is a month, as was said-- four seasons in the MBTA. Some agencies have more. Some have less. Winter, spring, summer, and fall.
And let's have a hypothetical workforce hiring scenario, where we hire up at the beginning of each timetable. We sort of run through the timetable. And then we hire up for the beginning of the next timetable.
That's sort of the hypothetical. That's not unusual. But it's not a very effective way of doing it. And what I've tried to explain here is why that is the case.
So the bottom bar in this graph indicates the timetable requirements. So typically, the timetable requirements for the operating plan are pretty similar across winter, spring, and fall, and they're lower in the summer. Why is that? No schools, and people on vacation, so your demand is generally down, unless it's a very strong summer tourist place, like Boston.
So that generally means that you can reduce your operating plan requirements in the summer. That is a wonderful. Why? Because many drivers would like to take vacation in the summer, OK.
I mean, unless you're a serious outdoor skier, ice skater, whatever have you in the winter, you probably don't want to take vacation in the winter because your children are still in school. Parents want to go on family vacations when the weather is decent.
So this cross-hatched area here is the vacation allocation you've made to fulfill your vacation liability over the year. And so what you see here is we're providing much more vacation in the summer than we are in the winter, or even in the spring and the autumn.
Why? That's because our demand is down, but the vacation demand is up. So that's a way of minimizing absenteeism. Makes our workforce happy, it's a good thing.
So this gives us this profile here about the number of people we need to cover the work and cover the vacations. So the only thing we haven't covered is the absence. And we have to cover the absence as well, because those people aren't there to work that particular day.
So typically, if you did this-- you hire up at the beginning of each timetable model that I talked about-- what you would have is something like this, in terms of the extra board coverage-- sort of a constant level throughout this, except at the end.
And the end of the timetable is higher because people have made changes and routes. There's retraining. There's training of new operators. So actually, your required work is greatest at the end of the timetable in the last three or four weeks. So that's what this jump here is, in terms of required work.
However, look at the supply. Typically what happens, is you have attrition over the course of the timetable. And you have increasing absenteeism over the course of the timetable. Why?
Because at the beginning of the timetable, people have just picked that work. They sort of want to do it. The grass is always greener. They're sort of enthusiastic at the beginning of the timetable.
They get out there, and they realize it wasn't all it's cracked up to be. And so when they're not feeling up to it, they're more likely to be absent perhaps, as time wears along. And then, towards the end, they've made their new selection of work for the following timetable. OK?
So what this suggests is you have a surplus of operators available at the beginning of the timetable and a significant deficit of operators at the end of a timetable. So you sort of have one day in the middle of a timetable, which is perfect. But otherwise, you're off. You haven't got this good balance between the operators that you have available and what you need.
So clearly doing workforce hiring every month, for instance, is one way of dealing with this. So you can reduce this hump for training new operators and spread it over the whole period because, in round terms, training for an operator takes about a month of on-the-road training. And so you spread that over the month, over the timetable.
So going to monthly hiring makes a lot of sense. And again, you avoid these problems having unassigned cover time. What that means is you've got people who are being paid not to be very productive in the garage.
You haven't got very, very good things for them to do. Because otherwise, you'd have built it into the operating plan. And large amounts of overtime and unreliability at the end of the timetable.
And I don't know what your experience is, but in my experience, that's exactly what you see. At the end of a timetable, service goes down the tubes, because you get this imbalance between higher absence and higher requirements for running into the next timetable. So you want to try and avoid that.
OK. So let's look at this from a total cost perspective. This is a very simple sketch. I'll show you something more realistic in a few minutes. But this is the conceptual part of this.
So on the x-axis-- and I apologize, this is a typo-- that's number of extraboards. The extraboard is the cover list-- the people who are there to cover absences or do extra work that's required not built into the timetable. These are extraboards or cover lists-- whatever. And that should be the number of drivers-- "extraboard operators," not "extraboard operations."
And on the y-axis, you have the cost. So if you have a small number of extraboard operators, your fringe benefit costs are low. Your fixed fringe benefit cost will increase as you increase the number. But you'll be relying very heavily on overtime.
So you'll be having high direct payment costs because of the reliance on overtime. And that gives you an overall high cost solution beyond some point where you get a good balance between the costs of overtime and the cost of fixed fringe benefits.
Then you'll get a sweet spot you'll want to try and operate. And you want to avoid this, where you've got so many operators that you've got a lot of people who don't have a lot of work to do on many days. Yes, question? Comment?
GABRIEL SANCHEZ-MARTINEZ: It's a question.
NIGEL HM WILSON: OK.
GABRIEL SANCHEZ-MARTINEZ: I didn't quite understand why monthly hiring would reduce the time.
NIGEL HM WILSON: OK.
GABRIEL SANCHEZ-MARTINEZ: Can you explain that?
NIGEL HM WILSON: Yeah, yeah. Sure. OK, so-- sorry, yeah. Thanks, Gabriel, for reminding me. It will take care of this hump at the end of the timetable. If there really is an extra requirement for work at the end of a timetable, you can hire up for that a month before.
So if you think of this as a sawtooth pattern, OK, which is what it is-- you've got attrition, and then you've got a bulk hiring-- if you reduce the periodicity of the saws-- the gaps-- you'll reduce the integrated imbalance between the requirements and what you need. So that's, in essence, what's going on here. Thanks. Good question.
OK so this is sort of the classic schema for analyzing this problem, for modeling it. So here on the x-axis, we have number of scheduled runs. This is for an organization that sort of looks a lot a lot like the MBTA.
And this histogram here is the cumulative distribution for number of absence days in the previous period. OK. So now we're running into the summer timetable for the MBTA. So when the MBTA was doing the analysis on this, they were saying, well, what level of absence can we expect this coming summer?
Well, we'll start by looking at last summer. That's probably a fairly good proxy for what we can expect this summer. And so the way they would look at that is look at the number of absent operators by day of week over the full range of experiences from last summer.
So on your best day last summer for the MBTA-- these are hypothetical numbers, but I want to give you the flavor of this-- you had 16 absences. 16 drivers didn't show up for work, for whatever reason. On your worst day, you had 60 operators who didn't show up for work that day. So it's a tremendous range. Question?
AUDIENCE: Sorry.
AUDIENCE: Yeah.
AUDIENCE: Can you explain how the chart works a little bit more?
NIGEL HM WILSON: Yeah. OK, so yeah. I'm trying to do a lot in one chance here. So this, if we look at that, it's the cumulative distribution of absence days. So this is the percent of days which have absences less than this number. So it's a cumulative distribution, cumulative density function.
So what we're saying here is that every day had no more than 60 operators absent. Every day had at least 16 operators absent. And this is the historical record of absences over that period.
Now, the reason I've drawn this line here is to show you what the extraboard sizing trade off is. So we're looking at, say, 31 extraboard operators here.
If we have 31 extra board operators and we assume there's no absence in the extraboard operators-- of course, there will be-- then we will be able to cover all of the absences in area B without paying any overtime. But all of the absences on days in area A, we'll have to pay overtime for, and we'll have to deal with reliability to drop trips on those days.
So the first point I want to make is this is a very simple model, but it's very useful. It provides a lot of insight into how you make these decisions.
The first point to make is, my god, that's a lot of variability-- from 16 to 60 operators absent on different days of the timetable. So probably some of that is systematic.
So some of them, probably you have maybe a higher absence on Mondays and Fridays than you have on Tuesdays, Wednesdays, and Thursdays. So you probably want to do this analysis at the day-of-week level, OK. Maybe you can group Tuesdays, Wednesdays, Thursdays. Maybe you can group Mondays and Fridays.
But the principles are the same. So there are different ways of classifying days to reduce the variance. But you're basically going to have this sort of trade off between your [AUDIO OUT] --terministic number from this cumulative density function, cumulative distribution. Is everyone comfortable with this? Because this is important. Yeah.
AUDIENCE: I'm just curious about-- so this is a broad spin on public transportation here. But I'm thinking of like delivery companies might be very similar.
NIGEL HM WILSON: Yes. Yeah.
AUDIENCE: [INAUDIBLE] consulted by them for this type of work? [INAUDIBLE]
NIGEL HM WILSON: I don't personally, but the problems are very similar. And the airlines have had very similar problems.
I was on a trip, not too long ago, where I was delayed at Logan Airport for an hour because they had an unexpected absence. Their reserved crew member happened to live in Nashua, New Hampshire, which a lot of airline pilots live in because it doesn't have any taxes in that state. And they had to drive down, in the peak hour, to get to the plane. I was delayed for an hour.
So every industry has the same sort of problem when it's a transportation industry, where you don't have a shelf life. It's not a production process. It's a service. And you have to deliver it at that time, in that location.
So there are similar problems. Again, it's not totally dissimilar from staffing in hospitals for nurses, for doctors, everything like that. So there's a whole class of problems here which are quite similar. And I'm just presenting the particular variant of this for the transit industry. Other questions or comments on this? Yeah.
AUDIENCE: Is this axis mislabeled here? Should it [INAUDIBLE] drivers, not scheduled runs?
NIGEL HM WILSON: Sorry. [CHUCKLES]
No. No, no-- it could be mislabeled. What I'm trying to say is, these are the number of scheduled operators who are absent on that day. That's what it really means, OK.
AUDIENCE: Runs for which the scheduled operator--
NIGEL HM WILSON: Yeah. So the analysis is the sort of full day for a full-timer. That's sort of the unit. And you can label the x-axis in different ways. And this probably isn't the best possible label. But that's what I'm getting at, OK. Other questions or comments?
OK, so let's quickly look at the strategic-level model here. Decision variables-- are what we're trying to decide is the workforce size for each period. And typically, as I said, maybe the period of a month, four weeks. And vacation allocation for each period and the vacation allocation will typically be over the course of a timetable.
So what's the average number of vacation weeks we want to provide in the summer at a particular garage or across the whole system? We'll provide the same number of vacation weeks for all the bus system in the MBTA.
And there's someone who's covering the vacation-- just is covering the different vacations every week of the timetable. So we have to have the same number throughout the timetable. OK?
And the optimal hiring level-- so you get the right number throughout the year. That's sort of what we're trying to achieve here. And the objective is to minimize the workforce cost, which includes the cost of the schedule runs, the costs of the extraboard-- the people who are there to cover the absences and the extra work-- and the cost of overtime.
And you'll notice there that I didn't include costs of reliability or unreliability, because I'm including that in the constraint. I could have included in the objective function. But I'm including it in the constraint, just because it's a little bit easier to conceptualize it that way.
And we were doing this work for the MBTA, who kind of like to think of overtime as a constraint. Because overtime, as you're probably aware, gets a lot of attention in the medial, in the press. You know, "10% of our budget is being spent on overtime for drivers." Those are headline sorts of issues.
So the MBTA and transit agency generally are sensitive to the level of overtime. That's why I structured this as a constraint, rather than as a multi-objective function-- [INAUDIBLE] multiple objectives.
Constraints we need to meet-- vacation liability, overtime service reliability, part-time operator constraint-- sorry. And any other policy constraints that we want to can be included in this optimization problem.
And the reliability model that we have is basically this. So what this is saying is we have open work. What open work means is we have work we want to do.
We don't have anyone who's going to be willing to do it without paying overtime. That's what I mean by open work. It's work that wasn't a regularly scheduled employee available to cover. So overtime is available.
If an operator is available and willing to work time, you come down here. And overtime is worked. That may produce more absence. May have those negative feedback effects. But at least you've delivered the service that day.
If there's no operator available or there's no operator willing to work the overtime, you drop the trips. And you've got a reliability problem on your hands.
Don't worry about the individual points there. But this is showing for the bus network on the MBTA, on the x-axis, the open work. This is for a particular timetable, system-wide for the bus, and the number of missed trip hours that were incurred that day. So each point here represents a day of operation on the MBTA bus system.
And so this particular day, you had close to 300 hours of open work. And you dropped close to 150 hours of service.
And if you do an OLS regression on this, this was the best fit we got. So that means for every 100 hours of open work at the time we did this analysis that you wanted to get, you were only able to get 72. And you wound up dropping 28 hours of service. That is pretty tough. That's actually really quite bad.
By comparison purposes, I've done other work in Montreal, Ottawa, and Toronto, which are pretty good, more or less, east coast properties. In Canada, they're never more than 10%.
So there's something not being done very efficiently in the way the MBTA covers their overtime. And I think part of this is probably over-reliance on seniority, again, and probably not doing enough advance planning.
And what do I mean by relying too heavily on seniority? How many phone calls do you make to the most senior operator who might be available before you say, he or she isn't going to do this work, and you go to the next person on the list?
And how much advance planning do you do to make sure that you've got a set of operators who are really going to be available if you have a need for them at 9 o'clock tomorrow morning? Those are the things that you could do to try and reduce this 28% missed trips to 5% or 10% missed trips, which would be a much better situation for everyone concerned.
So this is the MBTA case study again. Bear in mind that this was basically mid 1990s. So it's 20 years ago. But also, believe me, nothing much has changed in this regard at the MBTA.
I'm not saying nothing's changed in the MBTA in any regard over the last 20 years. But certainly in this regard, nothing much has changed. And I think there are still some of the same problems that I'll talk about here still in existence, which is sad for me to admit because, obviously, I was trying to help them-- didn't succeed.
So at that point, the part-time workforce was sized to about 40% of the full-time workforce. That's a little bit lower now, I believe. There's a large variability in required work hours.
So what do I mean by that? The mean daily absence and extra work required-- this is apart from the timetable. So this is shuttling service when you get a line down for signaling problem or disabled train or whatever it is, or fatality on the tracks.
The mean daily absence and extra work for the whole MBTA bus system was 1,250 hours on a daily basis. And the standard deviation of that was 290 hours.
AUDIENCE: What percent of that is total hours?
NIGEL HM WILSON: It's coming up. I'm getting into it in a few minutes. But round figure's 10%.
AUDIENCE: Wow.
NIGEL HM WILSON: It's pretty high. That's not just absence. It doesn't include extra work. OK?
AUDIENCE: But it does include sick leave, as well?
NIGEL HM WILSON: Yes.
AUDIENCE: OK.
NIGEL HM WILSON: Yes.
AUDIENCE: Any kind of absence.
NIGEL HM WILSON: Yes. Any sort of absence, exactly. So it's not in any sense absenteeism. It's the amount of extra work you have to do beyond what's the scheduled work, the scheduled operating plan. But anyway, it's quite large, and it's very variable. So it is highly stochastic.
Now, these figures were from 1996. And so the numbers will have changed significantly over the last 20 years. But the relative ratio of the numbers in the different columns and cells has not changed significantly in the last 20 years.
So what this is saying-- what we're showing here is the driver cost per platform hour. And so this includes the wage rate and benefits-- fixed and variable fringe benefits. So an hour of overtime worked by a driver at that time was around $30 an hour.
So sorry, the first row is the wage rate. The second row is the full cost. So the difference here is the benefits that are included, and the productivity changes between overtime, part-time, and full-timers.
So for overtime, you get a very small benefit load because most of the benefits are covered through their base job, OK. So the marginal cost of overtime work in terms of the benefit load is quite small, in the order of less than 10%-- or just about 10% of this. Whereas for part-timers and full-timers, full-timers get somewhat greater benefits. So it's a significant increment.
So if you just scan across here, this gives you the straight, direct comparison between the cost of an hour of work produced on an overtime basis by a full-timer or by a part-timer.
And in round terms, you say, well, if it's 40% part-timer, 60% full-timer, as the mix of workforce, versus $32.72 for an overtime, it's a wash. It's basically the same. OK.
So strictly in terms of cost, it doesn't really matter. It matters a lot if you have far too many people. But it doesn't matter too much in terms of the cost if you have about the right number or slightly less than that number. If you have a lot less than that number, the short-run financial costs won't change, but you'll have reliability problems because you won't be able to get the overtime.
However, what we really should be looking at is the marginal cost of the last person on the cover list. That's where we're making the marginal decision about whether we want to increase the cover list by 1 or decrease it by 1 or hold it where it is.
So if the last person on the cover list is being used 50% of the time, then you're making a trade off between $32.72 for an overtime hour versus $69.56 for the marginal person on the cover list.
OK, so what a critical issue is, in terms of any of you guys doing analysis for transit agency, be it JR-East or the MBTA or whatever it is, in this area, you really want to look at what the distribution of the costs are of the cover list.
And a good proxy for that is who's picking the work on the cover list. If it's the most senior operators who are picking the work on the cover list, that means that's pretty easy work. If the senior operators are not picking the cover list and it's being left to the junior people on the seniority list, that means the senior operators want to avoid it because it's difficult work.
So that's a sort of very simple shortcut-- do we have an oversized cover list or an undersized cover list? Look at who's picking that work on the cover list. Is it very senior operators or not? Any questions on this?
AUDIENCE: So cover lists-- are those people who come in, and they're sort of waiting to go on a [INAUDIBLE]?
NIGEL HM WILSON: Yeah. Yeah.
AUDIENCE: They're not people who are sitting at home, waiting for a phone call.
NIGEL HM WILSON: No, no, no. They're in the garage-- maybe playing cards in the garage. But they're in the garage, and they're available.
AUDIENCE: OK.
NIGEL HM WILSON: OK. OK, so I'm not going to go through the model. Again, I'm happy to give you the papers and theses on this.
One of these theses was done by Haris Koutsopoulos, who many of you know quite well. He's a senior faculty member at Northeastern.
Another of the theses was done by Yoram Shiftan, who was entertaining me in Israel just three days ago. So there's some very good work that's been done on this.
But the model that came out of this-- I'm going to go show you some results and talk about what they mean. What this is showing is, under different scenarios, the number of full-time operators, the number of part-time operators that produce the optimal solution, the overtime as a percent of the full cost-- the full cost, $96.4 million in this case, per year.
Sorry, that's the regular cost, regular time cost. It's the overtime cost. You add them up, and you get the total cost-- $97.8 here. And this is adding different constraints.
So the base case, without any constraints beyond vacation or liability-- the things that we've already talked about-- are that the cost of the MBTA bus drivers should be-- these are 1996 dollars again-- but $98 million.
And the reliability, given 1.5% of the time has to be worked on overtime, and given the way they manage their overtime, which is not very good, not very well, they'll be dropping about 0.4% of the trips-- 4 trips out of every 1,000. That was their existing level of unreliability in terms of dropping service.
So that's the base case numbers. You could then add different constraints. If you add a constant hiring constraint, which means that we hire the same number of operators every month over the course of the year and we don't allow it to vary from month to month, what does that do?
It makes it easier for the human resources folks. It makes it easier for the training people, because they know what their load is going to be throughout the year. And in fact, you can incorporate that single constraint with zero impact on the budget or reliability.
So the solution is exactly the same. We've just juggled vacation liability between different periods. OK? If we wanted to have a constant vacation as a policy in the organization, we add that as a constraint-- so the same month vacation throughout the year-- then that would result in about an almost $2 million increase in the total cost of the MBTA bus drivers.
We'd have less overtime. And so our reliability would improve to dropping 2 trips out of every 1,000, rather than 4 trips out of every 1,000.
And if we included in them both the constant hiring and vacation, which I don't think you'd want to, but this is just to show what you can do with this sort of model, then that would increase the budget by an additional $1.5 million a year.
And because you'd be relying less on overtime, you'd be having even more reliable service. So it gives the MBTA managers a sense of the trade offs here, but between the size of the workforce optimally structured over the course of the year and reliability and overtime.
One different set of results here. This is showing, OK, so what happens if we change the level of the overtime constraint? So the base case here is 1.5% time as a constraint.
If we just eliminated the overtime constraint completely and said, just choose the amount of overtime that gives you the minimal cost solution, then your overtime costs would be close to $12 million a year. And that would enable you to save about $1.3 million per year on the overall budget, because of the relative costs of overtime versus regular work.
However, your reliability would go to hell in a hand basket. And you'd be dropping 3 trips out of every 100-- 3 hours of service out of every 100.
And probably, this is much better than it would really be if you did that. Because this is not a linear function, OK. You're going to have more and more trouble covering those trips and getting people to agree to work overtime if there's so much overtime being asked of the workforce. So this is a gross underestimate.
But if you looked at 5%, which is still pretty high, then you'd save, in theory, about $800,000 a year-- less than $1 million a year. And your reliability would decrease significantly from dropping 4 trips out of every 1,000 to dropping 120 trips out of every 1,000-- no, 12-- from 4 to 12.
And then if you tighten the overtime constraint for whatever reason, then this is what it would cost you. It would cost you about half a million dollars a year. And again, you get some improvement in reliability.
So these are the sort of uses of the model that you can use to inform management decisions about how you structure your hiring process and training process and extraboard size. OK. That's all I want to say on the strategic level. Any questions? Yes.
AUDIENCE: Do you have a sense of how difficult it is or how costly it is to hire additional, new drivers?
NIGEL HM WILSON: Yes. Yes. So there is a training period. The MBTA, since Fred was Secretary, has had a lottery process for selection of new employees. And every agency, including the MBTA, has a pretty rigorous testing procedure you have to go through to get to the point of being hired.
You then go through training, the criminal records check, all sorts of checks before the training begins. And then the training-- I'm trying to remember, I don't have it on top of a head-- I think that the total training is in the order of six weeks, which includes getting your commercial driver's licenses, as we talked about earlier.
So you've got a certain amount of advance planning in here. You can't decide today, I want to have more people on the driver workforce tomorrow. It's not going to work. So that's why you need to have a strategic view of this. Yes?
AUDIENCE: Does this model capture the behavioral feedback loop?
NIGEL HM WILSON: It does not. So that was separate work. And we did look at that. But it's not in the results I presented. Though, as I said, Yoram Shiftan looked at feedback effect between if you provide more overtime, what does that do to absence?
And what he found was, it's variable. For some operators, there is a feedback effect. But it's not as strong as you might expect, OK.
So the MBTA management, for instance, was pretty convinced this was really a serious issue. It wasn't, in our analysis. But there is a feedback effect. It's not reflected in here. Yeah, Scott.
AUDIENCE: Earlier, you said you look at the seniority of the extraboards that are taking work from the cover list.
NIGEL HM WILSON: Yes.
AUDIENCE: And you said it's approximately more than the work that's desirable, right?
NIGEL HM WILSON: Yes.
AUDIENCE: The more senior person takes the work from the [INAUDIBLE]?
NIGEL HM WILSON: Yes, yes.
AUDIENCE: And I didn't quite get the implication there for the amount of work, [INAUDIBLE].
NIGEL HM WILSON: OK. So yeah. So if the most senior operators-- who can pick anything-- are picking the extraboard, that means you don't have to work very hard in the extraboard. The extraboard is probably too large. OK. That's the simple proxy.
Similarly, if the most senior operators are picking certain duties in a garage in terms of the types of shifts and the days they work, that's a good proxy for what's easy, what's not so easy.
That's not to say senior operators aren't highly motivated. They are. But they also have their own self-interest at heart. They don't necessarily want to be on a dangerous, difficult route to operate.
Now, the problem here, which Fred will get into I think next week, in terms of the way the US transit industry operates-- there are lots of problems. But one of the problems in terms of the way the US transit industry operates, compared with European industry, is they rely very heavily on seniority.
So what does that mean? It means the least capable drivers, who are the people who are new in the job and haven't got a lot of experience, have the most difficult assignments. That's almost certainly not optimal. So it means you have very poor drivers, in terms of not their capability, but where they are on the learning curve, driving very difficult routes.
And the European approach to this is typically to have a rotating roster, OK. And again, in the US transit industry, one of the main benefits of more seniority for a particular individual is you get to pick your work, and you get to pick your vacation time.
So if you get to 10 years at the MBTA, perhaps you never have to work weekends unless you particularly want it, which you often won't. Whereas in most European systems, you're assigned to a roster that rotates. So you will all go through the same experience over the course of two months. I don't know how JR-East does it, Kenji.
AUDIENCE: Similar to Europe.
NIGEL HM WILSON: Similar to Europe. That's really the dominant model elsewhere that I'm familiar with. There are trade offs in this.
So one of the trade offs is that if you use that as your main motivation for keeping people on the workforce-- you want to keep your good operators working, you don't have to replace them-- you can either pay a wage rate incentive for longevity, which is more common in other agencies around the world. But it's not very common in the US.
And so you progress from the entry level wage in the MBTA to the top level in about two years. OK, and that's not unusual in the US transit industry.
And so because that is such a minimal incentive to hang around for 20 years, you want to provide other incentives. And so seniority, picking your work, picking your vacation, is the way the US transit industry has followed this. Gabriel, you were going to make a comment.
GABRIEL SANCHEZ-MARTINEZ: It's a half-comment, half-question.
NIGEL HM WILSON: Yeah.
GABRIEL SANCHEZ-MARTINEZ: But when we discussed crew scheduling, we briefly touched on rostering and differences between North American and European practices.
NIGEL HM WILSON: Yes.
GABRIEL SANCHEZ-MARTINEZ: And well, part of that was that in European practice, rostering is done sometimes with some help of alarm or helping them to make the different rosters as even as possible.
NIGEL HM WILSON: Right.
GABRIEL SANCHEZ-MARTINEZ: And that is slightly different from picking them.
NIGEL HM WILSON: Yes.
GABRIEL SANCHEZ-MARTINEZ: Right, so in North American, these rosters are formed by people, but then they assemble the rosters from crew schedules. Is that correct?
NIGEL HM WILSON: Well, the roster, as I'm describing the roster, is the rotation, if any, of the work that's done among individuals over the course of a period, maybe a timetable or two months. If you have a rotating roster, that means everyone in this group goes through the same set of driving responsibilities over the course of a two-month period or a timetable.
In the US transit industry case, you don't have any rotation. You don't even have a roster. So you're there, you do the same trip every day if you show up for work. If you don't show up for work, you don't do the duty.
So it's a trade off. Personally-- maybe it's my European roots-- I kind of tend to prefer a European approach to this than the US approach to this.
OK. Let me quickly jump into the tactical level. So here, we're going into the summer timetable the MBTA in about a month's time.
And so we'll be deciding. We know how many drivers we have on the property. What we're deciding now is when to assign the work on a daily basis and how many operators to provide to Lynn versus Quincy versus Arborway versus Cabot-- the different depots in the system.
And again, so we're allocating the extra staff, these floaters, by garage and by day of week. And so we want to know the absence level on a more detailed basis here.
We have basically the same sort of issues and concerns, just at a more detailed level of analysis. And we can either use a heuristic or optimization for this. And heuristics actually give you a very good solution because it's much simpler.
This is real data from the MBTA, again, from 20 years ago. So I'm not saying it's exactly the same today. But I would bet it's not that different from now from what it was then.
So this is a single MBTA garage. This is the Cabot garage, which is one of the biggest MBTA bus garages. And for that garage, this shows the mean number of open hours of work on a daily basis over a timetable.
So on Mondays, 259 hours was the mean number of hours you had to cover because you didn't have someone available. Standard deviation of that was 36. So that's quite variable.
Tuesday and Wednesday is lower in terms of absences-- also quite variable. Thursday and particularly Friday is much higher and also even more variable.
So following our analysis principles, the cumulative density function, then you would expect to want to allocate your workforce, your spare workforce, reflecting the level of absence. But no.
The MBTA was allocating their extraboard exactly equally across all weekdays-- 20 extraboard operators on Monday, Tuesday, Wednesday, Thursday, Friday, Saturday-- Wednesday, Thursday, Friday, lower levels on Saturday and Sunday, but the same percentage, independent of the observed level of difference in absence or extra work required on those days.
The model showed that if you optimally reallocated the same level of resources, basically the same level down here in terms of operator days, you provide more cover on Fridays, on Mondays, and weekends, and less coverage on Tuesdays, Wednesdays, and Thursdays, reflecting the absence patterns. That's optimizing the daily level for a particular garage.
And at that point, they weren't using part-timers. They were using part-timers, but the part-timers were not on the extraboard and not being used in quite the same way that they are now.
And what you get out of this is the expected overtime hours over the whole timetable, recognizing the variability on a particular day is the expected level of overtime hours over the whole week is 140 hours versus 99 hours.
So you're saving about 25% to 30% of your overtime costs, just by reallocating your existing workforce more effectively across days of the week. This is not rocket science. This is actually pretty easy to do. I mean, you can get these absence figures quite easily and implement them.
So the tactical level findings are significant variation, absence, and required extra work by garage and by day of week. So what would you expect by garage, in terms of absence rates? You might expect-- and you'd be right-- that the most difficult garages would have the highest absence rates. Those are tough conditions.
So if you look at Cabot, those are very tough routes. And so when you do a system-wide pick that allows the operators to select the garage they work at, so the most senior operators will avoid Cabot.
So it's the most junior operators that wind up at Cabot on the most difficult routes. Not a great surprise your absence rate is higher at Cabot than it is at Lynn or Quincy-- nice, comfortable suburban garages. Yeah.
AUDIENCE: How do you define a difficult route? What constitutes [INAUDIBLE]?
NIGEL HM WILSON: Oh, OK. So there can be any number of things-- very heavy traffic, danger of accidents, danger of assault, crime, danger of altercations among customers, passengers on the bus, altercations with the driver. So a number of things like that.
And so I'm not saying all the routes in the Lynn garage are great routes. But compared with operating in the inner city, which is where the Cabot routes typically serve, there is a difference. And certainly in Quincy, there will be a big difference as well. Yes?
AUDIENCE: So the workforce would have differing levels of information about which route or which garage would be more difficult [INAUDIBLE]?
NIGEL HM WILSON: By word of mouth. It's not a sort of a conscious campaign. The idea is basically, you say, hey, we've got a seniority system. So you'll get to know other operators of different depots, word of mouth. And you'll select, based on what's available when it gets to you of your place in your seniority list, where you want to work.
And often, it's based on where you live. You don't want to have to commute from Lynn to Quincy every day to do your work. So it's a question of proximity to where you live and the ease, the comfort level you'll have on the routes and the conditions that you'll be operating on. OK?
And the policy of the MBTA at this point was to provide the same level of cover at every garage. Why? Their argument that they articulated to me-- and obviously, I discussed this with them extensively-- they would not dispute the fact that Cabot has a higher level of absence than Quincy or Lynn. They accept that. That's not in dispute.
But their argument would be, you're rewarding the manager of Cabot by giving them more manpower if you recognize the existing absence level. So they're concerned about this feedback loop. If you have more absence, you get more manpower.
To me, that's a completely backwards way of thinking about this. You need to have incentives for the managers to do a good job, hopefully. But you shouldn't let that be the motivation for making bad decisions about how you use your resources, which is basically what's happening here.
And they were arguing the same thing in terms of day of week, as well. So they were really fighting that, that concept. And I wasn't successful in persuading them that they should really separate out the management incentives from the efficiency of the decisions they're making.
OK. All right. The final level-- I've got a few minutes left-- is the operational level. So again, we've gone from the one-year planning horizon to the timetable planning horizon for three or four months, now down to the daily level.
OK. So the objective here is pretty much the same thing. We're trying to minimize the weighted sum of overtime and missed trips. Oh, I'm sorry. I'm still at the operational level here. Yeah, no this is right, sorry.
So what we want to do here is decide the report times for any unassigned, extra staff for the next day. So as I said, at 12 o'clock today, if there were five operators who had not been assigned work for tomorrow at Cabot, then the MBTA manager-- desk superintendent or whoever you want to call him or her-- at Cabot will be posting the report times for those five people tomorrow.
You don't know what the absence is going to be. You didn't have any known in advance absence to give them work to cover. But you want them to be available so that when you do get the absences, which you don't know about, they will be in a good position to cover them.
And so this gets into the most detailed level of this. So it's not just a question of having the right number of drivers available on a particular day. It's a question of having the right number of available drivers at every time of that day.
That's the problem we're dealing with here. So again, much more uncertainty about how the absence is at 9 o'clock AM versus 5 o'clock PM.
And what this is showing is this glorious concept. It used to be called "slop overtime." The MBTA didn't like the term "slop overtime," so it's now "excess overtime."
So you have regular overtime, which is just, you didn't have enough personnel on the payroll. And so you had to buy overtime if you were going to deliver the service.
Excess overtime is where, in theory you have enough people to cover the needs, but they're not available when you want them to be, because you couldn't make perfect decisions about when they should show up to make sure they're productive.
So here, I'm showing, here, this is time of day from 5:00 AM to 1:00 AM the next morning. This shows the open run profile, OK, like that. Sorry, this is the open run profile like this. And this is the available cover profile, based on your report time decisions, like this.
And so what this shows is that you have these periods here and here and here, where you had more operators available than you had work to cover. And so that means that there were other periods of the day here and here and here, where you didn't have enough operators.
You had the right number on the whole day, you just didn't have them at the right time in the day. And it's not just you made bad decisions, it's that this is stochastic.
You can't make perfect decisions. So you've got to expect there's going to be some excess overtime built in here.
And this is the excess overtime curve. And I will wrap this up in four minutes, I promise. I may not go through everything. But I'll cover most of what we want.
So this, on the x-axis, is the available cover minus the required cover. So again, if it's a perfect balance, excess cover minus required cover is 0 because you had a perfect fit. But what that gives you is the greatest number of excess overtime hours. Because unless you made every decision perfectly, you're going to have excess overtime hours.
If you go way out here, you had far more people available than you needed. So you shouldn't have any access overtime, even if you make lousy decisions.
You put them out any time, they'll be covered. And you put them out-- if you have far fewer people available than you require, you'll be out here. And you shouldn't have any access overtime either, because you don't have to be very good to make decisions which will have these people be fully employed. OK.
So it's when you have this exact balance, you have to make every decision perfectly to avoid excess overtime. And you're never going to do that.
OK, so I've got some results here, which you can go through on your own. And I don't think I need to cover this specifically.
But let me get to the conclusion on this. The analysis we did on this level of the model shows, because of the natural peaking in work requirements, that you have much more service in the peak than in the middle of the day, the base, it doesn't matter that absence rates are actually higher in the peak than they are in the middle of the day.
Because your decisions are driven by the same underlying dynamic. And so you just can make good report time decisions, based on the average absence rate on that day at that depot. So you don't have to go into super detailed analysis, which is good news.
And in fact, you can wind up with having a ranked list of report times that the desk manager at Cabot can just work off that list for tomorrow, based on the number of unassigned cover operators you have. And it will always give you a good solution, as opposed to the desk manager making decisions de novo, every day. This is a very simple decision support tool that can help.
So the operational level findings-- significant improvements are possible, can reduce the overtime and missed trips, and a single set of report times can be used across all weekdays and seasons for each garage. Separate ranked report times for Saturdays and Sundays, and constant absence rates can be assumed by hour of day and day of week. Those are the main conclusions.
OK, sorry I raced towards the end. But I'm available. I am retiring, as Gabriel well knows, at the end of the summer. This is probably my last lecture as a non-retired MIT faculty member. It's been fun doing it with you.
And I'm around. And I will be around after the end of the summer as well. Just I won't be being paid by MIT. So if anyone wants to discuss any of this or go through any of the background topics, please feel free to come see me. OK? Thanks very much.
[APPLAUSE]